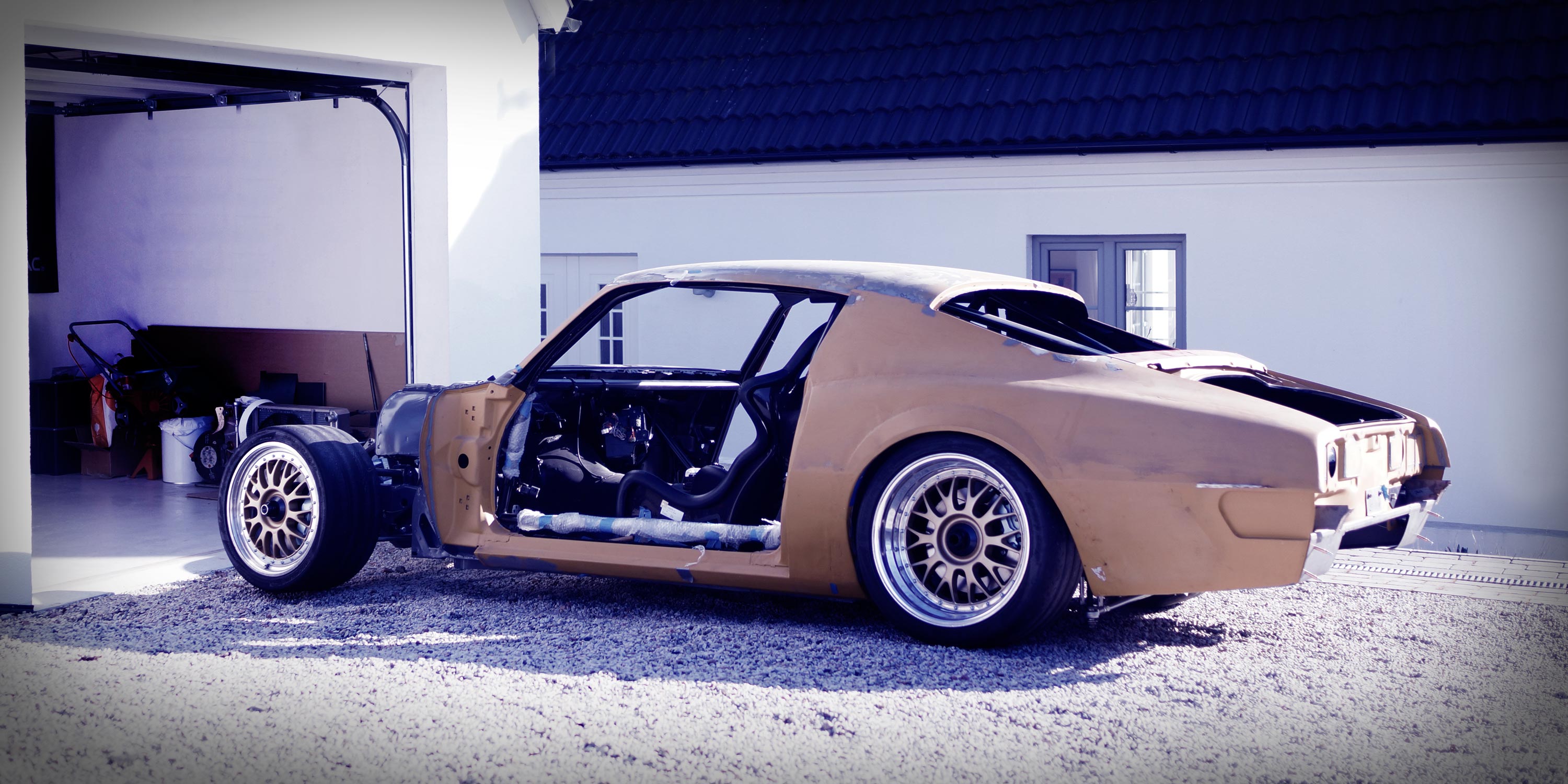
Kategori: The Project
Bränslepump
Som med allt annat blir det special hela tiden…
Här är bränslepumpen, en Walbro 255, som kommer monteras inuti tanken. Så mycket som möljigt hamnar i tanken för att inte sprida komponenter i onödan. Risken om något skulle läcka blir mindre, samt ljudnivån från pumparna blir också mindre.
Ovan; Bränslepumpen monteras internt. Lägre ljudnivå och skulle den börja läcka så blir läckaget internt i tanken istället för i bagaget. Känns bättre. Det blir en del special – Pumpen är förvisso standard. Kopplingen för att mata pumpen med bränsle är ganska hemmapysslad dock. Själva banjoskruven har fått hålet uppborrat för bättre flöde. Slangen är 10mm, och till M10 banjoskruvar finns bara 8mm slangfäste i vanliga affären. Med andra ord får ett fäste för 12mm väljas istället… och adaptrar (i aluminium, som glödgats efteråt för att bli mjukt) tillverkas.
Högra bilden: Fräsig AN-koppling köptes på trycksidan för att kunna använda rör upp till tankflänsen (även den egentillverkad eftersom hålbilden för pumpar, nivågivare etc blir special…). Även där var så klart hålet för litet. 60 sekunder senare i svarven så är hålet större.
Nedan; Även utloppet från catchtanken fick en egen dimension på slanganslutningen. Pumpen monterad på catchtanken i medföljande vibrationsskydd (blir intressant att se om det tål bensin…). Mer om catch-tanken nästa vecka.
Speciallösningar tar en hel del tid. Egentligen är det sällan själva tillverkningen som tar tid, utan snarare komponentletandet – försöka hitta komponenter i rätt dimensioner innan man ger upp och tillverkar eget…
Vibrationsfri tillvaro
När man investerat i så pass dyr elektronik får man göra sitt bästa för att skydda den så gott det går. Bilmiljöer är ju trots allt ganska krävande när man tänker på vibrationer.
Ovan; Eftersom stolen på passagerarsidan är långt tillbakaflyttad tillverkades ett nytt fotstöd. Som av en slump, blev det ett dödutrymme bakom fotstödet vilket passade utmärkt att användas till att fästa PDM-box och ECU på. SmartWiren (PDM-boxen) sattes på gummikuddar då den är något tyngre än ECUn. När det gällde ECUn användes istället samma typ av lösning som man ser inom motorsporten – gummisnodd.
Nedan; för att kunna låsa boxen med O-ring 3D-printades lämpliga fästen (som vägde in på 16 gram stycket – plast är fantastiskt!). Därefter tejpades ytorna med EPDM-list och sen var fästet klart.
Nedan; …och ECU.
Nedan; Det nya elutrymmet i kupén. Fotstöd på ena sidan och ellåda på andra. Passagerarstolen är monterad direkt på golvet (inget justerbart underrede ger lägre vikt, samt lägre placerad passagerare = lägre tyngdpunkt) och fotstödet funkar bra för personer upp till typ 190cm.
Uppmärksamhet
Det här projektet väcker faktiskt lite uppmärksamhet utanför denna bloggen också.
Senast i raden är Turnology.com som skrev en artikel om projektet nu i veckan. Är du följare av denna blogg är det ju egentligen inget nytt. För mig är det dock en bra egoboost och motivationshöjare att få läsa om sig själv i tredje person.
Tidigare har även Build-threads.com och Speedhunters skrivit några rader:
http://www.speedhunters.com/2014/11/iamthespeedhunter-the-creators-theme/
Elporr
Det är ganska ont om mumsiga köpta delar i det här projektet eftersom det är så mycket som byggs själv. Men när det kommer till elsystemet beslutades det om att stora lädret skulle öppnas. Hela Pontiacprojektet initerades i samband med att ECUn till motorn gick sönder. Det var inte det som väckte tanken om att bilen skulle modifieras, men det kan betraktas som ett startskott (eller en spark i häcken om att det var dags att komma loss).
Med andra ord behövdes även en ny ECU införskaffas.
Eftersom kunskaperna i mekanik är betydligt bättre än i el, kunde även lite fler inköp motiveras än bara ECU…
ECU:
Valet föll på DTA S80 PRO från det brittiska företaget DTA. Det finns nyare system också, men DTAet har rätt mycket extrafeatures, det kommer löpande uppdateringar med nya funktioner till mjukvaran samt att det passade budgeten. Förutom att hantera bränsle och tändning, kan det även sköta saker som elvattenpump, fläktar, AC mm. Dessutom finns det godsaker så som Launch Control, möjlighet att skifta mellan bränslemappar utan att koppla in dator, Traction Control, Shift Cut osv. Ja, typ sånt som alla ECU:er har nu för tiden…
Instrument:
Analoga mätare i all ära – det är fruktansvärt snyggt, passar bra i en klassisk bil och… sa jag att det var snyggt? Behöver man se fler än fyra mätvärden blir det snabbt många mätare dock. Istället för detta kan man använda en display och presentera den informationen som behövs. Tyvärr är de flesta dash:ar inte grafiska, utan fördefinierade områden används till viss information och vill man tänka utanför boxen kör man ganska fort in i väggen. DTA råkar, av en händelse, ha en riktigt fin dash i sitt sortiment – Grafiskt uppbyggd vilket innebär att man själv bestämmer var på skärmen informationen skall synas. Utöver detta kan den även presentera varningar för gränsvärden tydligt (tex över hela displayen), inte bara mätvärden utan även summan av ekvationer kan visas och en rad andra funktioner. Tex: givare i främre och bakre bromskrets och plötsligt kan man räkna ut skillnaden och illustrera hur den justerbara bromsvågen är inställd på skärmen. Dessutom ”råkar” den ha CAN-kommunikation från ECUn, dvs en enkel kabel mellan ECU och Dash och all informationen finns på skärmen utan att dra extra kablar från alla givare osv.
Nackdelen är att Dashen egentligen inte är särskilt prisvärd (läs dyr… nej… läs vansinnigt dyr) och hårdvaran kickas enkelt av vilken padda som helst numera – eller vad sägs om hissnande tvåhundrafemtiosex färger att välja på för skärmen? Det kan dock räcka ganska gott och väl för den typen av grafik som man behöver i en bil.
Fördelen med långtidsprojekt är dock att det ibland dyker upp helt OK deals från folk som säljer av delar. I detta fall dök det upp en säljesannons på rejsa.nu med ett ganska OK pris för en obegagnad dash (jag fick den stora äran att dra bort skyddsplasten från displayen).
PDM-ECU
När det kommer till resten av elsystemet känns det ganska 1900-tal att sitta och koppla reläer och säkringsboxar nu när så fina elgrunkor köpts in. Efter mycket övervägande köptes faktiskt en PDM-box (Power Distribution Module) som enklast kan beskrivas som en PLC för bilmiljö. Den var inte billig, men ack så smidig pryl jämfört med ett traditionellt elsystem.
30 kanaler ut och 10 in (ytterligare 20st in kan kopplas på) täcker det mesta, även om tex enklare saker så som backljus, bromsljus mm sannolikt kommer hållas utanför i dagsläget.
Grundidén med boxen är att man kopplar alla funktioner till den (knappar på ingångar och tex bränslepump på utgång) och därefter enkelt konfigurerar relationen mellan in- och outputs i mjukvara. Förutom detta finns det såklart en rad andra fördelar eftersom man jobbar med mjukvara, eller vad sägs om;
Vill jag att boxen själv ska nolla ”säkringen” några gånger innan den varnar för att vara säker på att det inte bara var ett temporärt fel? Check!
Vill jag övervaka strömförbrukningen på bränslepumpen och varna om den tex. skulle avvika 13% (för att förutse att den håller på att gå sönder)? Check!
Vill jag automatiskt stänga ner alla onödiga funktioner om spänningen skulle sjunka under en viss nivå (trasig generator) så jag kan ta mig hem? Check!
Vill jag stänga av ACn när gaspedalen är 100% för att få max effekt? Check!
Vill jag bara kunna använda mitt egenbyggda lyftsystem i tex 30km/h och under? Check!
Vill jag ställa fördröjningar för tex hur lång tid vattenpumpen är påslagen efter motorn stängts av baserat på vattentemperaturen? Check!
Mycket av ovanstående är såklart görbart genom att koppla reläer, motstånd osv. Men fördelen med mjukvara är ju utbyggbarheten – att man kan börja med standardsystem och lägga på funktioner allt eftersom man lär känna bilen, utan att för den delen behöva rota i det fysiska elsystemet på bilen.
Övrigt:
Elsystemet blev ganska dyrt (en tredjedel av den totala bilbudgeten! Dock fler prylar än det som syns på bilden ovan inräknat), men tycker man det är tråkigt att bygga elsystem, måste man ju motivera sig med exotiska prylar. Det fanns dock fortfarande lite pengar kvar i den numera slimmade plånboken, vilket lades på en rejäl sortimentlåda för Weather Pack-kontakter.
Även lite hemligheter så som spårsystem, startspärrar, larm och andra skydd för den klåfingrige kommer så klart hamna i bilen. Men den typen av uppdateringar hamnar tyvärr inte här. Stöldskyddet blir i alla fall hyfsat high tech det också, även om planerna på tårgaspatron i kupén och okrossbara rutor har lagts ned…
2015 – nöjd med insatsen?
Ännu ett år passerat utan att bilen blivit klar… Å andra sidan var det inte planerat att den ska bli klar detta året. Inte 2016 heller för den delen.
Tittar man tillbaka på 2015, så ser det nästan likadant ut som i januari vid första anblicken. Kan ju kännas lite hopplöst när man tänker på det så. Men det saknas ju trots alltid lite på bilderna som hunnits med under året – en genomgången motor med nytt oljetråg, bursträvor och andra förstärkningar i motorrummet, komplett styrning, ett fungerande bromssystem, avgasssytem, p-broms och en rad andra mindre arbeten. Mycket av ovan byggt från grunden (när man väl börjat finns det inget bolt-on som passar längre).
Nästa årsskifte kommer den säkert se ut ungefär som idag, men förhoppningsvis är första provturen tagen. Även om den bara är på gårdsplanen.
Ovan; Bilder från januari 2015. Allt sitter ihop, men mycket arbete kvarstår för att färdigställa hjulupphängningarna.
Årets stora händelse är ju i alla fall att bilen har varit nere på fyra hjul och till och med vistats utanför garaget vilket nog var största ego-boosten på flera år. Först när den kommer ut utanför garaget inser man hur låg den är.
Bilen har inte bara sniffat friskluft, utan den har även fått klä upp sig i ytterkläder för att kontrollera lite frigångar, att hjulbasen faktiskt var rätt osv. Spontana utropstecknet var hur långt bak motorn hamnade – den går knappt att nå från framsidan, utan man får stå på sidan för att komma åt. Det får plats en världsdel, eller åtminstone en atoll från lämpligt ö-grupp i Västindien, mellan motor och front. Inga problem med att få i en stor kylare med andra ord.
Ovan; Garaget är så litet att det knappt går att få plats med hela bilden i kameran. Får lokalisera en lämplig vidvinkelglugg till kameran när karosspanelerna kommer på för gott.
Nedan; Karossdelarna mättes in och det kunde konstateras att framhjulen sitter som en smäck o hjulhusen. Här är de fullt utfärdade och samma modifiering av hjulhuskanterna får alltså göras här som bak (dvs höjda dem). Det kom ju knappast som en överraskning dock. Skönt dock att bredden stämde (även om den kanske kunde varit 5mm smalare totalt, men det är för lite att bry sig om) och nu är det dags för att demontera alla punktade detaljer och helsvetsa dem.
Under 2016 är den startad och förhoppningsvis har det börjat hamna lite karosspaneler på den!
Växellådsbalk
Original växellådsbalk löper mellan subframebenen, dvs den är dryga metern bred och alltid ett helvete att få ner eftersom den sitter ovanpå rambenen och därmed måste snedställas. Men det går inte eftersom det sitter en växellåda i vägen…
Tidigt i projektet konstaterades det att det löper en tvärgående balk i karossen som kunde agera del av en ny växellådsbalk. Genom att nyttja denna, kunde den nya växellådsbalken göras kortare. Ca 25cm istället för 1,4 meter(!), vilket inte bara sparar vikt, utan även värdefullt utrymme för avgassystemet.
En liten fin laserskuren byggsats, levererad av hovleverantören (stort tack!), som kompletterades med två rörstumpar resulterade i en balk som väger drygt 2kg (original landade runt 8kg).
Ovan; Inspiration om att man kunde göra så här kom från någon bild från Speedhunters på en bil jag inte kommer ihåg vilken den var. Med motorn på plats byggdes en enkel mockup som sen mättes upp i CADen för att kunna skära till något snyggare.
Nedan; Balken i karossen hamnar på perfekt avstånd för att agera växellådsbalk. Hål kapades för att hysa infästningar, som självklart svetsades dit monterade i en fixtur för att det skulle hamna 100% rätt.
Ovan; Färdigsvetsad balk. Liten avvikelse fick göras för att optimera utrymmet för avgassystemet – Hela motorpaketet är flyttat ca 30mm åt passagerarsidan vilket plötsligt gjorde att förarsidan hade hur gott om plats som helst för avgassystem, medans passagerarsidan inte hade något. Det löstes genom att helt enkelt fasa den (det är alltså gjort på bilden…).
Nedan; Monterat och klart. 8.8-skruvarna skall bytas mot 12.9 med tiden. De fästelement som finns att köpa i järnhandeln är rätt tråkiga så planen är att köpa ett par kilon från lämpliga donatorbilar på närmaste bilskrot.
Hydraulikpump
Till lyftsystemet behövdes såklart en lämplig hydraulikpump också. Inte bara det, utan såklart även en massa komponenter i form av ventiler, styrningar till dessa osv. Hydraulik är inget jag har pysslat med tidigare, och som en ängel steg ner från himmeln, hörde en före detta garagekollega av sig och undrade om jag ville ha en komplett hydraulikpump från en palldragare. Tämligen bra timing och ett obeskrivligt stort tack!
Så, det som doneras till projektet är alltså ett komplett system med reglerventil, pump, elsystem och en kolv modell biffigare (som inte behövs, visserligen). Väldigt smidigt och det är i princip så nära ett plug-and-play-system man kan komma när man bygger själv.
Ovan; En bild på skönheten. Lite rörigt som synes, men det ska nog kunna fixas till. Kolven demonterades och hamnade i bra-och-ha-arkivet.
Nedan; Men ser det inte lite rörigt ut på bilden ovan? Systemet har ju suttit installerat i en annan applikation och då behöver det snyggas till lite innan det matchar kraven för Pontiacen. Bland annat 3D-printades en ny plastbit (vänstra biten, vid tummen) för att fästa säkringshållaren mot och som i sin tur kunde fästas på solenoiden till motorn. Notera att klickfästet mot särkingshållaren till och med funkar – inga engångslösningar här inte.
När man ändå var igång, var det lika bra att inkludera ett fäste för kontaktdonet också. Den skarpsynte noterar också att kablaget är lindat med lite vulktejp för att inte vara så spretigt.
Ovan; Slutresultatet. Antagligen hade det funkat med andra lösningar också, tex elhydrauliskt servo från någon lämplig bilmodell. Men denna lösning känns betydligt smidigare med tanke på lite klena förkunskaper kring hydraulik.
Nedan; Fäste mot karossen byggdes också ihop. Vart ganska pyssligt, men blev bra till slut. Istället för att fästa pumpen direkt i karossen och tro att man ska kunna hålla pumpen inuti kupén samtidigt som man petar i skruvarna från bagaget, gjordes en adapterplatta.
Ovan och nedan; Installerat och klart – Med tanke på vikten (7kg), har pumpen placerats så långt ner det går och mellan hjulaxlarna. För övrigt ett riktigt skit att försöka få en bra bild på det – allt är svart vilket innebär långa slutartider, vilket i sin tur kräver stativ, vilket i sin tur begränsar vinklarna från hur det är rimligt att rigga osv. Får överväga lite extrabelysning inför framtida kupéarbeten.
Pumpen monterades inne i kupén pga platsbrist. Det fanns visserligen plats i bagaget, men bakom bränsletanken. Dvs för att komma åt pumpen behöver bränsletanken demonteras. Känns sådär spännande. På sikt skall även brandsläckningssystem placeras på denna plats och när det blir dags för inredningsjobb kapslas allt med lämpliga paneler.
Slutligen, stort tack för donationen av Marty!
Det här med låg bil…
Att en låg bil främjar köregenskaperna vet de flesta. Lägre tyngdpunkt kortar hävarmen mellan rollcentrat i hjulupphängning och tyngdpunkten bland annat. Låga sportbilar som bara körs på slät asfalt (banor tex…) har egentligen inga problem med att de är just låga. Låga sportbilar som rullar på gata har en massa problem dock. Kommuner och deras vägbulor bland annat.
Istället för att försöka övertyga landets alla kommuner om vägbulornas negativa miljöpåverkan i form av ökat slitage på däck, bromsbelägg, ökad bensinförbrukning, svårt för utryckningsfordon att komma fram osv får man ta saken i egna händer. Superbilstillverkarna har redan löst problemet genom att kunna lyfta sina bilar några centimeter och det bör ju kunna appliceras på entusiastfordon också.
Ovan; Hydrauliska kolvar som lyfter bilen 50mm. Tillverkade i aluminium och därefter eloxerade. De levererades till mig av Ajdén monterade, vilket kändes väldigt lyxigt. Det mesta till den här bilen har ritats, byggts och monterats av undertecknad varför det ibland är skönt med saker som kommer färdiga…
Jag teamade upp med Ajdéns Mekaniska & Motorsport för att ta fram ett lyftsystem som kunde monteras på vanliga coil over-dämpare. Robert Ajdén bygger själv en kopia av Le Mans-vinnaren Bentley EXP Speed 8 och hade liknande problem som jag med markfrigång. Jag har konstruerat åt oss, och Ajdén har sedan tillverkat. Grundtanken var att sälja den här typen av kit, men prislappen blev ganska hög (som tre knäckta fronter ungefär…). Så projektet stannar sannolikt vid de prototyper som har tillverkats hittills.
Det ligger en hel del arbete och tankeverksamhet bakom dem, så räkna inte med några snygga CAD-genomskärningar eller andra beskrivande bilder. Dock är det inget hokus pokus heller. Enkelt beskrivet; hydrauliska kolvar som lyfter bilen totalt 50mm. Kolvarna kopplas till en hydraulpump som aktiveras när det behövs.
Ett smidigt sätt att överleva med låg bil i stads-vägbule-djungeln.
Kopplingspedal
Pontiacen hade hydraulisk koppling redan i förra inkarnationen. Dock blev det aldrig riktigt 100% och kopplingen var rätt tungtrampad pga onödigt dålig utväxling på pedalen.
För att komma till rätta med detta, har en ny slavcylinder införskaffats som är anpassad för cylindern nere vid kopplingen. Bara kvar att hitta en lämplig plats för den med andra ord. Tyvärr innebär placeringen att; om ett bromsservo skulle behöva adderas i framtiden så skapar det problem då cylindern kommer sitta i vägen för detta. Men vi lever i nutid och vissa saker får man blunda för (även om misstanke om behov av bromsservo finns…).
Ovan; En simpel mockup byggdes för att kunna lokalisera rätt höjd på cylindern och kontrollera att inget tog emot. När detta var gjort, spikades placeringen i sidled genom att finjustera distansen på pedalen. Som synes blir det en distans (på bilden temporär för att hitta rätt höjd…) mellan cylinder och pedal för att få ut den på rätt plats. Kopplingspedalen är dock tämligen styv eftersom axeln för både bromspedal och kopplingspedal är svetsad i den sistnämnda och därefter lagrad på två punkter i pedalstället. Jag är inte så orolig för snedbelastningar med andra ord.
Nedan; När koordinaterna var fixade, användes den temporära mallen för att kontrollera på in- och utsida vid torpedväggen för att se att den gick fri. Det gjorde den. Bara och börja borra med andra ord. 22mm stegborr räcker inte långt när man ska upp i 33mm. Resten av hålet handfilades upp.
Nedan; Hål taget, och cylinder monterad. Blev rätt bra. Ska fixa ett par aluminiumplåtar att lägga mellan väggen på in- och utsida för att sprida ut kraften lite bättre på torpedväggen eftersom plåten bara är 1mm gods. Muttrarna mellan torpedvägg och cylinder försvinner då alltså…
Bromsvåg och pedalställ
Bra bromsbalans mellan fram och bakhjul innebär bromsvåg. Detta hade ganska enkelt kunnat integreras i bromspedalen vilket inneburit att cylindrarna kunnat skruvas direkt på torpedväggen. Det innebär dock att om man någon gång skulle vilja gå tillbaka till servoassisterad bromsfunktion så får man börja kapa och svetsa i torpedväggen vilket kanske inte alltid är så kul. Det finns ändå en risk/chans att bilen kompletteras med servo i framtiden om pedalen skulle visa sig vara allt för tungtrampad.
För att både kunna äta kakan och ha den kvar letades en box, där vågen installeras i, upp. Grundtanken var att tillverka en egen (så klart!), men denna Sellholmbox dök upp på en säljesannons till ett överkomligt pris.
Ovan; Tanken var alltså att det skulle se ut så här om det var hemmagjort. Nu trillade det ju in lämpliga detaljer i färdigt skick, och då kändes det inte lönt att gå sin egen väg längre…
Ovan; Wilwoodcylindrar i lämpliga diametrar, samt Sellholm box.
Nedan; Cylindrar monterade och även en bild på delarna installerade. Orgie i egentillverkade prylar… Vippan till själva bromsvågen fick tillverkas och skymtar på bilden. Även axeln till hållaren. Eftersom jag bara hade tillgång till metriska brotschar (att ta upp hål i vippan med) fick det tillverkas ett nytt rör till bromsvågen som hade metrisk utsida. För att inte få in damm eller motorljud i kupén, användes en gummibälg från MecMove. För att få denna att sitta fast mot torpeden, 3D-printades en fläns att fästa dem mot som i sin tur skruvades mot bromsvågen. Många detaljer som knappt syns när det väl är klart.
Nedan; Färdigt. Även bromsrör på plats. På bilden syns även lite andra prylar -3D-printade hållare till dämparresevoarerna och kopplingscylindern. Den sistnämnda kommer lite mer om nästa vecka.
P-broms… Det går bra nu…
För den som tror att det bara är att ”bygga ihop” en bil med egna komponenter är det ganska fel. CAD, misslyckade försök, ny CAD, misslyckat… Ny CAD, prov i verkligheten, tillbaka till CAD osv. Tålamodsprövande det här med att bygga bil.
P-bromsen är inget undantag. Den fick aldrig riktigt vara med på ritbordet utan vilket egentligen aldrig var meningen. Det bara blev så. Sånt får man sota för i efterhand genom extra arbete och anpassningar. Bilderna visar bara ett första misslyckat försök. Grundtanken var att försöka belysa att det ofta ligger väldigt många försök bakom egenutvecklade prylar, men kameran fick inte riktigt alltid följa med på alla försöken… Misslyckat försök att försöka visa misslyckade försök med andra ord.
Ovan; Försök 1 blev någon form av skruv i befintligt fäste på spindeln. Ganska lagom placering på hålet i förhållande till var armen på oket hamnar. Dock känns konstruktionen något klen och vajerdragningen efter spindeln och längs karossen är fortfarande ganska oviss.
Nedan; Dock blev i alla fall vajerdragningen från infästning och upp till ok väldigt bra. Kylkanalen till bromsskivan fick bändas lite i sidled. Bromsvajrar är faktiskt original till bilmodellen (trummor med andra ord). Fjädern på vajern är för trummorna. Jag har låtit den sitta kvar, då längden var förbluffande lagom och den faktiskt tvingar tillbaka bromsarmen vilket gör att… Ja, det känns bara bra helt enkelt.
Nedan; Försök två blev egentligen en vidareutveckling av försök 1. En platta som sprider kraften på två skruvar, samt lite justering på infästningen för att inte vajern ska krocka med dedionen.
Högra bilden visar den fantastiska anledningen till att om man ska rita prylar i CAD, ska man rita allt. Även fästelement. Oket kunde placerats 10mm längre bakåt egentligen, men nu hamnade det där det hamnade. Lagom mycket i vägen för att vara för lite i vägen för att egentligen orka bry sig. En fil löste biffen även om det är principiellt fel.
Nedan; Monterat på bilen känns det ju såklart väldigt bra. Till och med vajern visar sig gå att leda någorlunda bra fram till originalpedalen.
Ovan; Så var det bara wiren som skulle dras också!
I en optimal värd hade allt byggs klart innan någon ytbehandling gjorts (karossen skulle alltså inte varit lackad än) och då skulle man såklart bara svetsat fast ett sådant här fäste istället. Nu fick det skruvas i karossen istället. Försänkt skruv på undersidan för att… öh, minska luftmotståndet eller nåt.
Nedan; Handbromswire infäst. Dragningen visade sig bli riktigt bra. I detta fallet ren tur snarare än framförhållning då P-bromslösningen som sagt gjorts efter allt annat varit färdigkonstruerat och tillverkat. En slangklämma håller fast wirehöljet för att avlasta infästningen lite och spara wirehöljet från knäckning eller liknande.
Även en drivaxel-mock kan skymtas på bilen. Mer om det senare…
Bromsar…
Med bromsar monterade var det dags att sätta igång med rördragning. Lite komponenter har handlats hem från andra sidan pölen. Försöker generellt använda samma komponenter fram och bak för att behöva ha färre reservdelar på hyllan. I detta fall blir det samma längd på bromsslangar fram och bak, samma anslutningar och samma rörnipplar i hela systemet. Alla relevanta prylar kan köpas som reservdelar i Sverige, men priserna råkar vara lite bättre i staterna så om inte tidspressen finns beställs det därifrån.
Ovan; Ett gäng komponenter från Speedway Motors i staterna. Alltid lika roligt att öppna påsar med nya, rena prylar i. Rostfria rör (blänker ju fint mot den sidenmatta RAL7015-färgen) istället för vanliga kopparrör. Man får hålla tungan rätt i mun så att man inte borrar hålen fel för komponenterna i nylackade prylar.
Nedan; Samma bromsslangar fram och bak, samma adptrar, nipplar, infästningar osv fram och bak. Ju färre olika komponenter desto enklare. Att dubbelkona rostfria rör visade sig inte vara det enklaste. Biltema-verktyget är att betrakta som en engångsartikel i sammanhanget. För att få tillräcklig klämkraft, fick det klämmas med hjälp av skruvstädet, och en egen dubbelkoningsfnutt fick tillverkas. Svårt att se fnutten på bilden nedan till höger.
Nedan; Rördragningen till bakbromsarna var lite pillig, men den följer väldigt nära golvet i alla fall. Funderade ett tag på att dra det inuti kupén istället, men det sitter rätt skyddat där det sitter på bilden så det blev undertill istället. Högra bilden visar slangdragning till bakvagnen. I vänsterkant av bilden sitter slangen i ett T-kors till rör som löper längs dedionen. För att inte få okontrollerad rörelse i slangen, begränsades den lite genom en hylsa (som den löper fritt i) som sitter mitt på. Det visade sig att hälften av slanglängden räckte (lika längd fram och bak för att förenkla reservdelslagret) och blev över för fjädringsvägen.
Bromsar bak
När det kom till bromsar bak gällde det att hitta något som matchade frambromsarna vad gäller kolvarea. Mestadels av lasten läggs på frambromsarna under retardation, Därför är inte styvhet riktigt lika viktig bak som på fram. Det tänkte jag inte på när jag handlade, utan kan snarast klassas som en efterhandskonstruering för att framhäva hur genomtänkt och perfekt det här projektet är…
Bakre oken var nämligen väldigt små (fysiskt) jämfört med framoken, som är gigantiska. Dock är undertecknad övertygad om att de kommer fylla uppgiften väldigt bra.
Ovan; Wilwood IR-GT4R. Rätt kolvdiameter, låg vikt och klarar nog jobbet som bakbromsar bra. 4-kolvsok har ju så klart inte någon P-broms… och det tycker ju SFRO är rätt bra att ha. Med andra ord köptes en uppsättning p-bromsok. Även dessa tillverkade av Wilwood. Sannolikt utvecklade av någon ingenjör som var trött på sitt jobb. Antagligen är det en cheddarluktande, engineer-Bob som tyckte det var viktigare att komma hem till grillen och dricka Bud än att göra bra produkter. Därefter har gissningsvis gjutverktyg varsamt tagits fram av slarviga små barnfingrar fem mil utanför en stad som inte Uppdrag Granskning känner till i Bolivia och till sist har en oförstående marknadsavdelning börjat sälja produkten utan att ens titta på den. Med andra ord som vilken vanlig manick ”made in the USA” som helst…
Nedan; Oken har fått en spacer monterad för att kunna greppa över de breda bromsskivorna. Eftersom det inte finns någon vettig infästning på dem har glidpinnar konstruerats. (många väljer att istället att montera oken stumt i en tunn plåt och sen montera denna i spindeln och låta plåten göra arbetet – jag måste ju så klart gå min egen väg och uppfinna hjulet på nytt istället… Hur var det nu med svenska, smörgåsbordsätande midsommarstångsdansande ingenjörer? De kanske inte är så mycket bättre än Budweiserdrickande jänkediton?)
Ovan; Ganska mycket TV-kocksvarning i dessa uppdateringar eftersom det aldrig visas någon action utan bara resultat, men så här blev det. Liten temperaturdekal på oket också för att kunna ha lite koll på värme… Temperaturskalan börjar på 100 grader, så svårt att ha dem som termometer på garagetemperaturen men förhoppningsvis kommer väl bilen ner från pallbockarna innan OPEC slutar sälja olja.
Nedan; I fantastisk kvalitetsanda visade sig hårdvaran till de fantastiska P-bromsoken kom så klart obehandlad i vanligt svartstål. De Aluzink-behandlades för att hålla lite längre än bara första provturen. Högra bilden visar bromsoksadaptern, en av få CNC-frästa detaljer i projektet. Även pegs och pinnbultar till bromsoket är CNC-svarvade, signerade ”Joakim”. Tack för hjälpen!
Wilwood förtjänar inte på något sätt ett dåligt rykte pga p-bromsarna. De är imponerande slarvigt tillverkade när man jämför dem med deras andra keramiskt coatade, unobtanium CNC-billettjohejsan megabromsok. Som med allt annat får man vad man betalar för och för 400:-/st kan man nog inte begära mycket mer. Framoken har ett listpris på 2800 dollar/st och P-bromsoken 99 dollar/paret som jämförelse…
Skulle det visa sig att de inte fungerar, finns det många standardbilar som använder liknande P-bromsok, Audi R8 tex. Prislappen är så klart inte 400:- (och vikten är betydligt högre…), så Wilwoodoken får bekänna färg först…
Ovan; Audi R8-ok (höger) samt Brembo eftermarknadsok (vänster).
Bromsar fram
Tidigare i våras skruvades bromsoken fast på spindlarna. Känslan av att skruva fast dem för första gången och det sitter perfekt centrerat och allt passar utan en enda provmontering tidigare – när man har byggt alla detaljer runtomkring själv är… obeskrivlig. Det är inte för att låta dryg som det tjatas om detta hela tiden, men det är en enorm kick att konstruera saker och sen få kvittot genom att det blir exakt så som man tänkte sig. (undrar om man får äta upp det där citatet efter första provkörningen?)
Bromsslangar krävde dock en hel del funderande för att få rätt på. Dels skulle längden bestämmas, sen kan inte slangen vridas, utan bara böjas vilket också ställde till en del. En del klurande i att få sånt att löpa fint.
Bromsarna förresten. Wilwood P6R (även kallade Prolite på vissa ställen). Magnesium/aluminiumhus med keramiskt coatade kolvar (för att inte överföra värme från beläggen) samt polerade, rostfria plåtar inuti tråget för att reflektera bort strålningsvärmen. Mums.
Ovan; För att inte slangen skulle ta emot någonstans och för att inte utsätta den för konstiga vridningar fick det experimenteras en hel del. Det slutade med att en position hittades där slangen behövde fixeras vid spindeln för att röra sig rätt. Med lite enkel hårdvara löstes problemet…
Nedan; Buntbandet på bilden ovan utbytt mot plåt och gummiklämma. När beläggen hamnar i oket, då känns det nästan på riktigt!
Ovan; På plats, äntligen. Bara att trampa på pedalen nu med andra ord.
Bromsar, renovering
Det här var ju (från början) ett budgetprojekt. Det är fortfarande ett budgetprojekt i form av att det går mycket arbetstid istället för pengar för att lösa problem.
Budgeten innebar att det var bara och glömma att köpa nya flashiga AP-ok, Brembo eller liknande. Och sexkolvsok måste det ju vara för det är ju… coolt.
E-bay dammsögs efter möjliga kandidater långt innan projektet egentligen påbörjades och ett par rejäla hejdare lyckades ropas hem för ett blygsamt kostnad. Som vanligt med begagnade prylar är det alltid bra att börja med att renovera dem, så slipper man strul senare längs resan. Bromsoken var inget undantag – nya O-ringar, ny ytbehandlning på alla fästelement, polering av värmeplåtarna och lite ny färg lyfte oken till nyskick.
Lekte även med tanken på att fräsa in PONTIAC på oken, men det föll på att det inte fanns någon gratis-tid i en CNC fräs någonstans. Budgetprojekt, remember?…
Ovan; När väl oken kom hem från staterna visade de sig vara betydligt större än förväntat. På den högra bilden står ett A4-kuvert i oket som en storleksreferens. I välkänt Wilwood-manér, har den svarta ytbehandlningen övergått till en lila-violett färg. Inte så lockande, så…
Nedan; …därför togs beslut att måla om dem. Plasti-Cote motorgrund och därefter Pontiacs motorblåa nyans som en liten hyllning till företagets glansdagar. Även fästelementen fick ny svartoxid då den gamla var rätt rostig på sina ställen.
Nedan; Antingen besitter undertecknad små nätta frökenfingrar, eller så har bromsoken kapacitet att stoppa vilket lok som helst. Det sistnämna stämmer bättre. Som synes på handleden är de inte fjäderlätta, men strax under 4kg/st får anses vara ok för ett så stort ok.