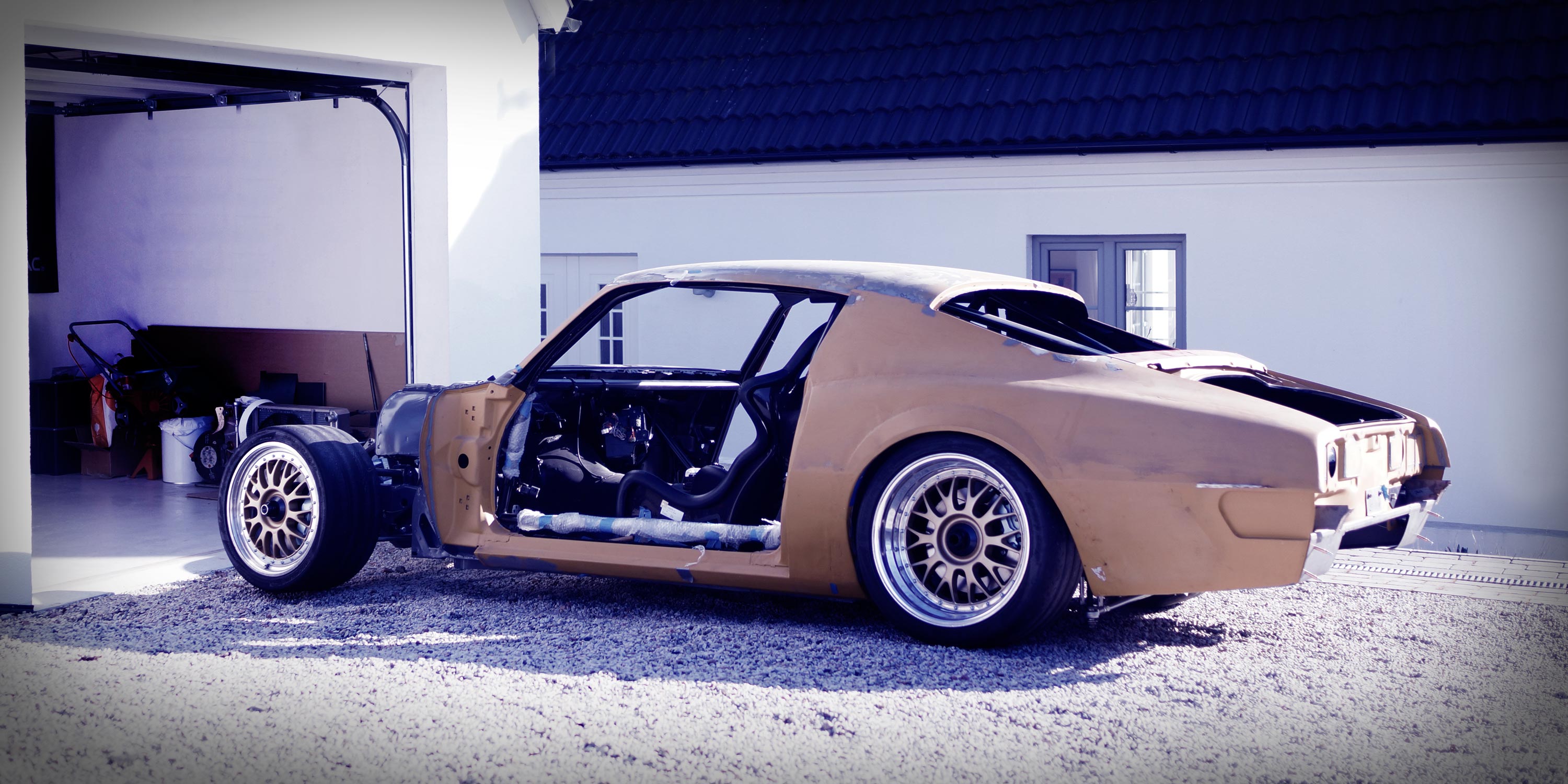
Kategori: Suspension
Kaross x (diffklump + dedion) = Passform?
Ovan; Ett försök att vädertäta länkarmsbussningarna har gjorts. I detta fall med det fantastiska och väldefinierade materialet ”cykelslang”. Just cykelslang brukar (endast i detta fallet, aldrig när det ska lagas punktering) ha den unika förmågan att vulka fast i det mesta. Förhoppningen är med andra ord att den med tiden kladdar fast i metallbussningen.
Nedan; Såklart är det inte 100% vattentätt, men det är i alla fall dammavvisande och stänktätt. Betydligt bättre än helt öppna bussningar med andra ord. Plastbuntbanden hoppas jag kan bytas mot något bättre på sikt. Tills vidare får det funka.
Nedan; Tredje länken monterades med hjälp av fyra händer. Skruven sticks i inifrån kupén, men någon måste ligga under bilen och hålla i länkaget. Förbannade konstruktörer – att de alltid ska krångla till det…
Ovan… och nedan; Med tredje länken monterad, provmonterades diffklumpen i karossen för första gången. Platsbrist mellan diffkåpa och dedion har skapat flera millimetermätningar på karossen, fullskalautskrifter av ritningar som måttades mot karossen och en rad andra sätt för att försöka säkerställa att sakerna inte skulle krocka med varandra när de väl kom på plats. Som skrivits innan är det alltid svårt när delar från verkligheten som är för komplexa att rita av (karossen…) ska linjera med konstruerade detaljer från datorn. Det är svårt att hitta lämpliga referenser, svårt att mäta exakt och symmetrin mellan höger och vänster sida på karossen är ofta obefintlig.
Men fega pojkar får aldrig pussa vackra flickor och bilbyggare som aldrig chansar är… öh. töntigt.
Hur som helst – det passar! Med kortast möjliga länkarmar är det ca 7mm frigång mellan diffkåpa och dedion – trots plåtförstärkningen som spontansvetsades på bakaxeln utan att tänkt igenom vad som riskerade att hända med utrymmet. För att hjulen ska sitta rätt i hjulhuset, kommer länkarmarna vara ca 20mm längre än i testläget, dvs där kommer finnas gott om plats för både bakvagns- och karossflex. Win med andra ord!
Nu blir nästa punkt att provfjädra dedionen för att se att det inte tar i någon annanstans.
Subframe, igen
Veckans jobb på framvagnen. Det mesta börjar bli färdigt nu.
Ovan; Anpassningar till befintlig ram kräver lite extra detaljer här och där. Gamla urtaget för styrväxeln har delvis fått läggas igen. Som om det skulle användas igen… Högra bilden visar att det faktiskt börjar bli klart – vipparmsinfästning och fästen för övre länkarmar.
Nedan; Vipparmsinfästningarna har svetsats både från in- och utsidan. Rejäl V-fog på utsidan och lika-bra-att-svetsa-här-också-fog från insidan.
Nedan; Även rambenen är numera svetsade som de ska.
Bara interfacet mot framtida kylarram kvar, sen är det dags för grundfärg!
Svetsning…
Det blir tämligen många meter svets när man håller på med plåtkonstruktioner… Vill inte riktigt räkna efter hur mycket det rör sig om, men det har uppskattningsvis tre 50-liters TIGtuber på att bygga fram och bakvagn och ett antal timmar. Bara ”de sista detaljerna” på subframen som pågår just nu har hittills tagit ca 100h att färdigställa. En grov uppskattning säger att byggtiden på subframen är runt 200h. Lägg därtill konstruktionstid i datorn också…
Ovan; Fixturen positionerar både länkarmsinfästningar och vipparmsmontage. Det är väl inte positionering på tiondelen med tanke på att det är vanliga fyrkantsprofiler, men det håller betydligt högre toleranser än vanliga biltillverkare gör på sina saker.
Nedan; Hade nästan vant mig vid att se ramen utan infästningar…
Coil over-infästningar och krängningshämmare
Lite prylar behövde tillverkas för att komplettera ramen. Infästningar för coil-overs och vipparmstornen.
Ovan; Börjar bli ganska bra kompis med TIG:en nu. Men å andra sidan har det spenderats ett par hundra timmar bakom den, så konstigt vore annars. Bilden visar infästningarna för stötdämparna. Samma princip som bak, dvs ett öra som håller coilovern (skymtar längst bak i bild) och som sedan kan flyttas fram och tillbaka på subframen beroende på längd på coilovern. På så sätt är det enkelt att uppgradera i framtiden utan att behöva göra stora ingrepp i chassiet.
Nedan; Krängningshämmare har det funderats på ett tag nu. Vanliga rörklamrar köptes från Swedol som lagerbockar. Därefter svarvades ändavslut (notera flänsen för att inte krängningshämmaren skall glida i sidled) som sedan parades ihop med ett 40x2mm rör. Ja, 40mm i diameter. Planen är inte att låta röret ta vridningen, utan istället tillverka knivar och därmed isolera rörelsen till dessa.
Nedan; Ytterligare en bild på coil over-infästningarna. Översta har även coil over-örat ställt ovanpå sig för att illustrera justerbarheten. 3 lägen totalt med 25mm mellan varje. 75mm längre/kortare dämpare kan med andra ord få plats.
Vipparmshylsorna fick så klart svarvas ur då de annars hade blivit löjligt tunga.
Subframe
Förhoppningsvis sista svetsjobbet på subframen har påbörjats. Infästningar för övre länkarmar, krängningshämmare, vipparmar, stötdämparinfästningar och för kylarram skall fixas. En liten diger lista som kommer ta ett antal timmar att beta igenom.
Det mesta har dock tänkts igenom under mycket lång tid, så förhoppningsvis är risken för tankevurpor minimal.
Kvar på att-göra listan är; Övre infästningar för länkarmar, vipparmsfäste, fästen för coil-overs, infästningar för krängningshämmare, hålbild i framkant för kylarram, lite blandade infästningar för smått och gott, motorfästen. Utöver detta finns det en del helsvetsning kvar att göra eftersom vissa delar bara sitter punktade. En hel del med andra ord.
Ovan; Först ut var att mäta hur mycket plats det fanns för stötdämparna mot torpedväggen, innan subframen demonterades. Det fanns ganska lite plats. GM räknade nog inte med push rod-konverteringar av befintlig framvagn…
Nedan; Den som inte kommer ihåg, så är det så här det är tänkt att bli…
Ovan; Fixtur monterad. Den bibehåller korrekta mått mellan övre och undre länkarmsinfästningar.
Nedan; Fixtur, samt laserskurna öron på högra bilden. De beställdes 3mm för långa egentligen, för att jag skulle kunna få en bra passform mot ramen. Ramen har ju varit lite svår att rita av i datorn, men det visade sig stämma på pricken! Hade de bara varit 2mm för långa, hade de alltså varit för små… Onödigt spännande med andra ord.
Bromsar bak
Även bakre bromsarna är monterade. Bellsen är egentillverkade och inte riktigt lika avancerade som de främre vad gäller interfacet mot skivan. Eftersom hålen i skivan är avlånga, räckte det med att ha runda hål i bellsen och ändå kompensera för värmeutvidgningen på skivan. Paketet låstes med låsmuttrar i stål.
Även pegs:en är klara. Fick dessa CNC-svarvade av en snäll person och de blev riktigt bra. En av få CNC-tillverkade detaljer i projektet. Det mesta är som sagt handjagat pga budgetkraven…
spindlar färdiga!
Äntligen! Spindlarna klara. Ett antal meter svets, därefter värmebehandling för att spänningarna skulle släppa, därefter fräsning av lagerytor mm. Hyfsat mycket arbete som sagt. Nu blir det provmontering av alla kringkomponenter innan det är dags för ytbehandling.
10kg skruv har även skickats på ytbehandling. Skrämmande hur många kilo fästelement det sitter på en bil…
Mäta mäta mäta…
Ovan; Mäta mäta mäta, sen fräsa några tusendelar i taget… Ja, presspassning är inte alltid helt enkelt att få till. Konsekvenserna vid en felkörning gör också att man inte bara tänker en, utan två gånger innan man tar ytterligare en hundradel…
Nedan; Men resultatet blev bra. Jag tjatar ofta om vilka möjligheter man har med CADen… så även denna gången. 4mm mellan spindel och skivan visade sig vara 4,05mm i verkligheten. Sakerna passar direkt, och sitter som man tänkt vilket är väldigt bra för motivationen (slippa göra om…).
Hjullager & Spacer
Arbetet kring spindlarna fram fortsätter. Hjullager kommer från Corvette C6 är planen för framvagnen. ABS-sensorerna kopplas till motorns ECU för att fungera som input för traction control, anti-spinn osv.
Ovan; Distanser till centrummuttersystemet. Små mästerverk i sig, särskilt om man tänker på att allt man ser är handjagat i en manuell fräs. Det har tagit sin tid att tillverka dem, och tittar man väldigt noga kan man se lite missar i sexkantshålet, som beror på sena kvällar och trög skalle… De fyller dock funktionen ändå och som sagt – de blev stiliga! Synd att de inte kommer synas…
Bromsar, fram
I början av projektet köptes begagnade Wilwood-bromsar från en Winston Cup (typ Nascar) bil. Wilwood P6R heter modellen, och är i dagsläget Wilwoods näst värsta modell. Ett sexkolvs Magnesium/alu-ok, med keramiskt isolerade kolvar och tunna, rostfria plåtar på insidan för att minska värmespridningen från skivan till oket. Modellen är rätt gammal, så i dagsläget finns det såklart ännu fetare bromsar hos andra tillverkare. Dock är dessa förhållandevis lätta och mer än tillräckliga för att få stopp på Pontiacen. Skivor kostar 120 dollar stycket och belägg kan köpas på e-bay för allt mellan 40$-100$, så driftkostnaderna blir förhållandevis låga.
Dubbla uppsättningar skivor och en rejäl kartong med olika hårda belägg har redan burits hem i handbagaget från USA-resor och ligger i dagsläget på hyllan som reservdelar.
Ovan; Det visade sig att det bara skiljde någon ynka millimeter på standardbells och de egenritade. Konstruktionen stretchades då till att tillåta standardprylar istället. Skivorna kommer obehandlade. För att hindra lite av rosten på de ytor som inte är beläggytan, målades dessa med Plasticote gjutjärnsgråa högtempfärg. Skivorna mäter 330x35mm. Breda doningar som ändå tillåter 17″-fälgar och till och med vissa 16″-fälgar (vilket var ett krav om man skulle vilja lämna 18″ till förmån för någorlunda originalstuk i framtiden)
Nedan; Wilwods låsningssystem ser lite roligt ut, men det verkar fungera eftersom de har haft samma under lång tid…
Montering, bakvagn
Det börjar ta sig!
Nedre länkarmarna sitter på plats. Den övre fick avvakta och blev istället i trä. Samma med stötdämparna för att få bakvagnen i ride height. Generellt är det en nästan euforisk känsla att få börja skruva på delar på bilen. Bakaxeln behöver fixas några mindre saker på, därav att den fortfarande är senapsgul. Ett tränat öga skymtar dessutom att växellådan sitter på plats till vänster i bild. Det går bra nu!
Montering, länkarmar
Bakvagnen gjordes klar förra året. Därefter har den legat i bitar och vissa detaljer lämnades in för ytbehandling. Eftersom det var gängor, interna ytor med presspassning osv. var det enklare att gulkromatera detaljerna än att lackera dem. Baserat på samma resonemang ytbehandlades även vantstagen (i aluzink) eftersom de har nyckelgrepp för justering.
En rad andra saker har också kromaterats och förzinkats istället för lackering. Dels är det snyggt och väger lite, men fördelen är främst att det täcker bra och är okänsligt för stenskott.
Ovan vänster; Vantstag hamnar närmare bakvagnen än karossen. Karossen var i vägen för att tex ha den mitt på staget. Högra bilden visar en del av den överkurs som görs i samband med projektet – självklart får det ju tillverkas ett verktyg för att kunna spänna bussningarna. Ytbehandlat och märkt med rätt bilmärke, så klart!
Subframe påbörjad!
Att hålla på med den här typen av projekt kräver en hel del planering, både vad gäller logistik, få hem köpta komponenter i tid, samt fördela resurser på det som för stunden är bäst. En enkel lösning hade varit att köpa hem allt direkt, men risken finns alltid att man ändrar sig lite under projektets gång och plötsligt behövs det nya delar. Dessutom binder det kapital, och om projektet av någon anledning skulle läggas ner, är det onödigt att tex sitta på 100 000:- i delar som är svårsålda. Utan att avslöja för mycket, är det en liten garageflytt på gång under vintern, vilket skapar lite oreda i planen. Plötsligt måste vissa som inte var lika brådis med färdigställas snarast. Bland annat måste subframen vara tillräckligt färdig för att kunna provmontera drivlina och tillverka motorfästen till denna. På bilderna nedan finns alltså fas1 av subframen. Utöver det som syns på bilderna, tillkommer övre länkarmsinfästningar, krängningshämmarinfästningar, burrör, vipparmsinfästningar och då såklart motorfästen. Dvs nu blir det motorfästen, resten kommer i framtiden.
Av besiktningstekniska skäl, återanvänds de längsgående rambenen (för mycket saker får inte ändras)… Egentligen skulle bryggan också användas, men den visade sig tyvärr vara för rostig kring infästningarna och arbetet skulle bli för stort för att rädda den. Därför föddes idén om en ny framvagnsbalk, vilket i sin tur tillät tillbakaflyttad motor, lägre vikt osv.
Ovan; Precisionen blir riktigt bra, trots den något primitiva fixturen. En fullskaleritning skrevs ut för att bygga framvagnsbryggan av. Därefter positionerades denna med hjälp av utmätning av centrum mellan infästningarna i karossen. Precisionen blev bra som sagt, uppskattningsvis mindre än +-1mm. Gissningsvis bättre, eller i klass med de stora biltillverkarna.
Nedan; Vänster; Vaggan ligger högre än de längsgående benen. Detta är pga de längsgående benen egentligen ligger för lågt, trots att de sitter så högt upp i karossen som möjligt. De får helt enkelt betraktas som skrapskydd för resten av underredet.
Ovan; Hålen närmast i bilden ska såklart läggas igen också. I övrigt ser den ju ganska stöddig ut, subframen. Lite mer triangulerat än tidigare och betydligt styvare.
Vaggan till framvagnen klar
I somras påbörjades framvagnsvaggan. Den har därefter fått ligga till sig lite pga andra prioriteringar i projektet, men nu börjar det bli dags för att färdigställa framvagnen också.
Den har på bilderna kompletterats med bakåtgående profiler där bla. bakre infästningen av nedre länkarmen hamnar, samt även motorfästen.
Ovan; Total vikt blev 11,0Kg, jämfört med originalbryggans 17,5kg som den ersätter. En rätt trevlig viktbesparing med andra ord, även om den råkar vara lågt placerad.
Nedan; Det som skiljer köpta komponenter från hemtillverkade är att man har möjlighet till längre arbetstid på de hemtillverkade. Mycket svets blir det…
Ovan; Alla infästningar görs i hylsor, som svetsas i båda profilerna. På detta sätt fördelas lasterna fint över ett större område. Bilden visar ett par hylsor till motorfästen. Även om de ”bara” ska svetsas, måste såklart kanterna brytas – något annat vore slarv.
Nedan; Färdigt resultat att svetsa på de längsgående ramdelarna. Blir bra det här…