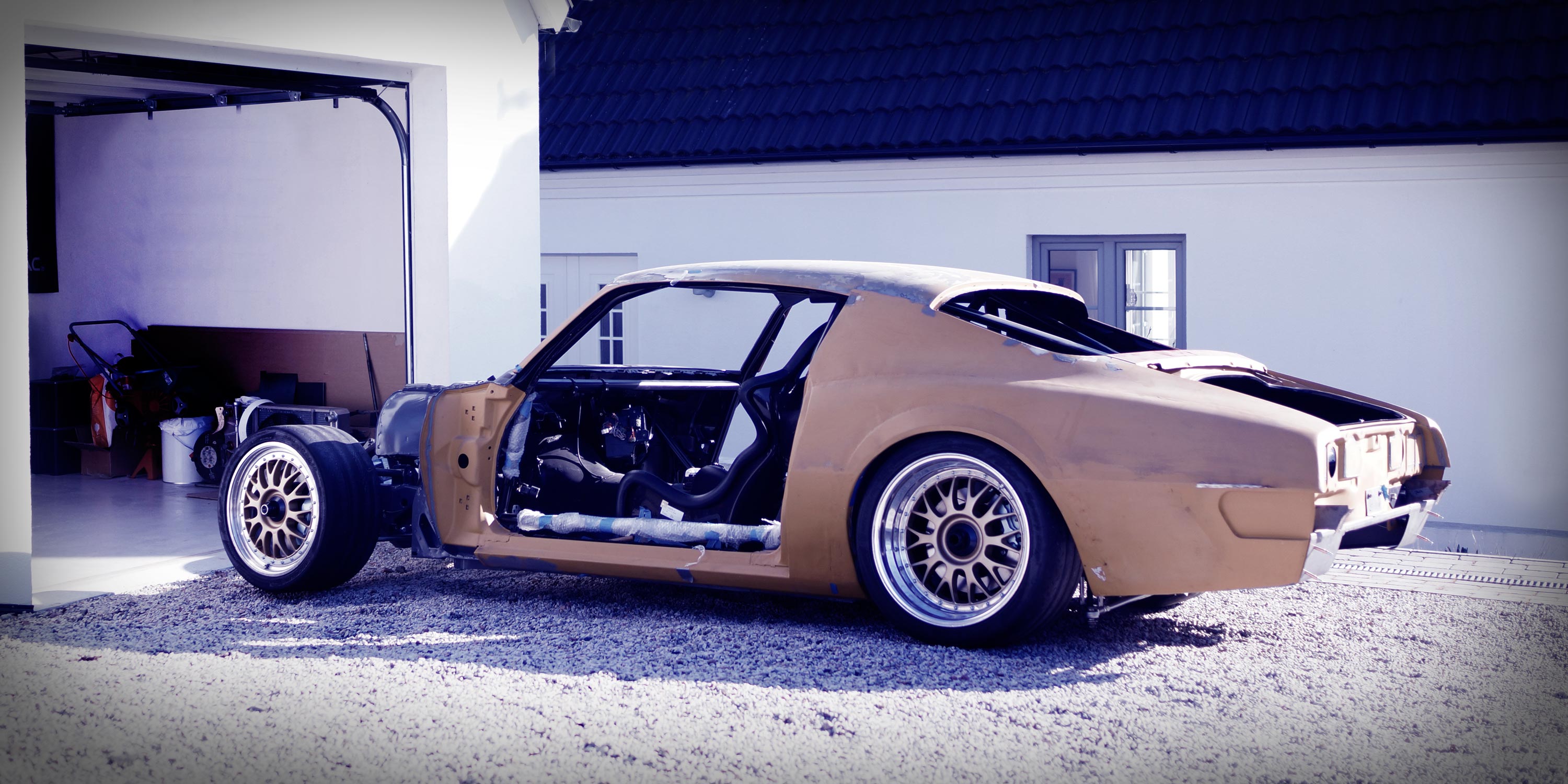
Etikett: TIG-welding
Kylarram
Hög på endorfiner efter den lyckade SFRO-besiktningen gick det såklart inte att ta en paus från projektet. Fräsen vevades igång samma natt som besiktningen gjorts och delar till kylarramen började komma fram.
Kylarramen har evolutionerats fram i tankarna under en rätt lång tid. Inte för att det är någon rocket science, men den kommer även bära front och skärmar så den får inte vara sladdrig, men gärna lättare än originalets 15kg. Självklart görs den i alu – samma typ av profil som karossvaggan byggdes av, och slutvikten uppskattas till ca 4kg totalt. Mycket fräsning blir det och alla uppspänningar var inte helt triviala.
Viss nervositet för att ramen skulle upplevas som sladdrig fanns såklart, men magkänslan säger att den borde vara tillräckligt styv. Borde. Det är visserligen inte värre än att man får tillverka lite nya bitar, men det är både trist att göra om saker samt att åka runt med för mycket dödvikt.
Ovan; Det blir färre och färre prylar som snidas med vinkelslip numera. Alu är dessutom inte något smidigt ämne att skära med vinkelslipen. Lite CAM-beredning och sen ut i fräsen och jobba. Svårt att spänna in en U-profil tillräckligt hårt på högkant, men det gick ganska bra.
Nedan; Ytterligare urfräsning för att vikten närmar sig noll. När den tas bort ur fräsen, får den knytas fast i arbetsbänken så att den inte svävar iväg.
Ovan; Man kan göra saker enkelt för sig. Sen kan man göra saker svårt för sig. I det här projektet är det ganska få saker som tagit den enkla vägen. Fräsningen av en 900mm bred profil i en maskin som max kan ta 300mm åt gången resulterade i fyra (eller om det var fem) olika CAM-program för samma profil och ett gäng omtag. Men vad gör det? Resultatet blev ju hur fint som helst!
Nedan; Lite känsligt med att placera saker nära marken framför framaxeln. Sånt tenderar att ta i marken…
Dock har det ju utvecklats ett lyftsystem som lyfter bilen 50mm vid behov, så det borde gå att kylarramen sitter på samma höjd som resten av chassiet – dvs 90mm över marken.
Nedan; Färdiga bitar som svetsas samman – det blir nästan som lego. Alu är lite svårare att svetsa än stål, men övning ger färdighet. Ser OK ut, men finns lite att träna på vad gäller genombränning osv.
Kardanaxel
Kardanaxel blir, som allt annat, speciallängd för att passa med den tillbakaflyttade motorn. För många år sedan införskaffades en Ford Motorsport 3″ aluminiumkardan. Den verkar hålla för de flesta Fordägarna (Fordägare brukar ha fullt upp med att få resten av bilen att hålla, så de kanske inte märker att kardanen också går sönder…) och med tanke på att Pontiacen blir så lätt att ankare behövs när den skall parkeras, känns det som den kommer leva ett ganska bra liv i Pontiacen.
Längden var ju så klart fel, och att få tag på någon i Sverige som kunde tänka sig att korta en aluminiumkardan visade sig vara svårare. Balansering gick att lokalisera dock, men då behövde den vara färdigkortad innan.
En utmärkt anledning att införskaffa en AC/DC-TIG för att kunna göra jobbet själv med andra ord. Kortningen blir ju ganska dyr om man tar med svetsen i kalkylen, så det får man helt enkelt låta bli att göra. En AC/DC maskin är ju dock något som är väldigt bra att ha, och nu när man äntligen hittat en anledning att köpa en gäller det att passa på. Blir nog inte sista aluminiumprylarna på Pontiacen…
Ovan: Patienten på (det kliniskt rena) operationsbordet. 137mm skall kortas, men det behöver planeras lite eftersom änden för knutkorset inte går att spänna upp i svarven.
Nedan; Änden uppspänd i svarven. Den får svarvas rätt från början (en tolk tillverkades för att hitta rätt diameter för röret) eftersom chucken håller på de sista millimetrarna (som får stickas av innan den plockas ur). Inget vidare enkelt att spänna upp den – Ford verkar slarvat från början, så hela änden kastade drygt en millimeter (men sånt verkar man glatt balansera bort i serieproduktion). Efter ganska mycket om och men satt den dock rätt i svarven.
Ovan; Hmmm, det är något som saknas på den här kardanen…
Den gör sig helt enkelt bättre som polerad!
Nedan; Omsvetsningen närmast diffklumpen – jag antar att Ford är bättre på att svetsa än mig, och då är sannolikheten störst att den går sönder i den nya svetsen. Går den sönder, är det bra om det inte blir ett spett ner i asfalten som sliter loss hela bakvagnsinfästningen. Har inte gjort något fäste för det, men gissningsvis kompletteras axeln med en fångring i framtiden, även om det känns lite dragracingvarning på den…
Nedan; Same but different, som kinesen hade sagt! Kortad, polerad och balanserad! Visade sig att det var obalans i båda ändar (skäms, Ford!) men det fixade Göteborgs Kardanaxelservice till. Visade sig vara ganska få som ville balansera aluaxlar (eftersom alla svetsar på stålvikter), men ovan nämnda företag verkar ha gjort ett väldigt bra jobb.
Dekaltrimning, ja… Hmm. De två svarta parallella strecken är för att upptäcka om materialet vrider sig med tiden (dvs om axeln är på väg att bli utmattad). Texten tillkom av bara farten. Kardanaxeln döljs effektivt bakom avgassystemet, så knappt ens besiktningsmannen kommer kunna se den…
Återmontering; Framvagn
Återmonteringen fortsätter – lite plåt trillade in för någon vecka sedan vilket gjorde att de nya länkarmarna kunde byggas klart. Snart borde bilen åter igen vara ihopmonterad och det blir mindre och mindre kvar inför första SFRO.
Ovan; Äkta pussel. Vinkelslipen kom inte fram en enda gång! Upp i fixturen med dem och börja nästa ihop delarna. Som vanligt är det ont om bilder när man befinner sig i stridens hetta, och istället får man hålla till godo med TV-kocksvarianten… ”Jag har förberett en färdig länkarm här på bilden nedan”.
Nedan; …men en bild hittades i kameran i alla fall, precis innan TIG:en sparkades igång.
Ovan; Inte VM i TIG-svetsning direkt, men det börjar ta sig (förutom vänster i bilden – där är det kräkfult. Fattar inte vad jag sysslade med…)
Nedan; Och monterat, men utan spindel… och i närbild…
Ovan; Allt på plats och inshimsat för första gången. Extremt tight – inte mycket flex i upphängningarna, trots polyurethanbussningar på ett par ställen. Känns bra. Höger bild; Pushrodsen åkte såklart med på helsvetsning också när länkarmarna fixades. Ett par M16-mutter svarvades ur och pressades på efter helsvetsningen, samt låstes med några svetsloppor för att kunna justera dem.
Catchtank
Catchtanken är i det närmaste klar. Kvar är att lösa ledning av påfyllningsröret och var tanklocket skall placeras, men det tar nog ett tag att klura ut (eller tills att det blir prioriterat i alla fall). För övrigt känns det väldigt bra att lyckats klämma in pumparna inuti tanken istället för att ha ett virrvarr av rör i bagageutrymmet. Pumparna sitter bättre skyddade, mindre buller, minskad risk för läckage och säkert någon fördel till.
Bränsletanken känns så säker den kan bli. Lite trist att åka omkring med 100L bensin om något skulle hända, men säkerheten är prioriterad så gott som det går; Plasttank med invändig gummiblåsa. Skum i tanken, främst för minimerad lastförskjutning men det rinner lite saktare ur tanken om det ändå skulle gå hål. De flesta komponenterna inuti tanken gör att volymen bränsle i ledningar utanför tanken kan hållas nere, samt kulor som stänger tanken om man skulle råka lägga bilen på taket.
Nedan; Blev faktiskt rätt fint i slutändan. Nivågivaren (röret till vänster) är visserligen för kort – längre modell var av en annan typ och kostade orimligt mycket pengar. Det får duga tills vidare, och istället bli ett uppgraderingsprojekt i framtiden. På bilden syns också förra veckans första CNC-frästa detalj – röret för att hålla kulan som stänger om man hamnar på taket.
Nedan; Livet blir enklare med en styrd fräs. 🙂
Alla hålen i plattan nedan kördes fram med fräsen. Röret på högra bilden känns säkert igen från förra veckan. Den är tänkt att hysa kulan, som landar mot det svarvade sätet om olyckan skulle vara framme och bilen bestämmer sig för att lägga sig på taket. Hålet för bränslegivaren (stort hål med fem små runt om) – ATL tog i och gjorde ett asymmetriskt bultmönster, men bara så lite att man inte märker det. Upptäckte det i sista stund och lyckades googla fram håldelningen.
Ovan; Så här då alltså… I hålet till vänster på bilden hamnar avluftningen. Samma funktion, dock köpt istället. Andra bilden visar genomföringarna till tanken. AN8 (1/2″ rör). Den lilla kopplingen kommer bli genomföring för elen.
Nedan; Tryck och returkopplingar. Fullradie för trycksidan för att maximera flödet (jo, här klyver vi hårstrån, jag vet…), och vanlig för andra sidan. Kunde såklart valt fullflöde på båda, men nu blev det som det blev. Tredje genomföringen blev lite hemmapyssel. Kontakt för bränslepumparna. Fylls med epoxi när det är tid för det.
Ovan; 3D-printat bränslefilterfäste, generation1 och generation2. Ettan var tänkt att nitas i plåten på bagagerumsgolvet. Efter utskrift, låg det och skräpade i garaget ett par månader i väntan på att bli prioriterat. När det var dags, kom det nya insikter och istället gjordes en variant som nyttjar befintliga hål för infästning av bränsletanken.
3D-printers erbjuder konstruktioner som annars hade varit omöjliga. Hålen man ser på bilden är genomgående och alltså spåret för slangklämman som skymtar nedan.
Kopplingarna borrades upp ytterligare ca 2mm i diameter och har blivit konade i ändarna för att inte strypa så mycket.
Nedan; Filterinsats. Vanligt Volvo V70-bränslefilter – enkelt att köpa på hyllan i Sverige de gångerna det behöver bytas.
drivaxlar – kortning
Svårt ämne det här – att korta drivaxlar. Det ses som hilly-billyteknik av många, medan andra alltid berättar om en kompis kompis som körde kortade drivaxlar på sin top-fuel dragster och som höll för ungefär åtta miljoner hästar i 200 år. Helt sant, kompis kompis så de känner typ oftast varandra. Nästan.
I detta fallet kan man se det från en annan sida; Bakvagnen är byggd från blankt papper. Där är inte så många saker som i teorin kan gå snett, men å andra sidan brukar det sällan vara de sakerna man aktivt förebygger utan de oförutsedda som strular i slutänden. Specialtillverkade är relativt dyrt – 6000:- för två stycken.
Att sortera ut bakvagnen tar gissningsvis 50-200 mil kanske innan man har säkrat att allt håller och fungerar som det är tänkt. Då är man sällan uppe i 250km/h. 0-100km/h under tre sekunder förekommer inte heller så ofta. 50-200 mil kan man använda hembygdda drivaxlar, och därefter kan de uppgraderas till specialtillverkade om man inte insett att hela bakvagnen behöver konstrueras om.
Nu behöver nog inte hela bakvagnen konstrueras om – men du fattar säkert – det finns en ovilja i att investera i specialprylar som kanske måste kasseras efter första säsongen. När allt väl fungerar, ska jag köpa drivaxlar som får Formel1-teamen att kännas som amatörer. Om man nu kan få sånt för 6-7kkr…
Ovan; En rad olika tekniker gicks igenom och via internet försökte förstahandserfarenhet sållas ut. Verkar som att vanlig V-fog och pinnsvets är en ganska tillförlitlig metod då pinnen skapar en förhållandevis mjuk och duktil fog.
Nedan; Sådärja, inget att be för. bara att såga av axlarna. Innan de kapades, rensvarvades de från tidens ytbehandling – rost alltså. Därefter V-formades de med vinkelslipen. Efter dessa bilder ökades V:et till ca 30mm/axel. Dvs fogen blev totalt 60mm bred – många svetssträngar blev det innan den var fylld.
Nedan; Svetsad och grovsvarvad. Rotation med indikatorklockan för att hitta var den slår (drivaxlarna svetsades spända mot en V-profil, men de slår sig lite ändå). När läget var lokaliserat, flyttades drivaxel och indikatorklocka över till pressen där den justerades. Det blev några vändor fram och tillbaka, men till slut slog de på mindre än tre hundradels millimeter.
Nedan; När axlarna inte slog längre, var det bara att svarva det sista och därefter slipa med smärjelduk tills att skarvarna försvann. Notera märket på svarvchucken för att alltid spänna in den i samma läge (eftersom den åkte fram och tillbaka mellan press och svarv).
Högra bilden, någon enstaka por här och där avslöjar att man meckat med axlarna, men annars är det svårt att se.
Nedan; Färdiga axlar, i väntan på lite färg. Så klart gick ett av clipsen som låser axlarna av vid demonteringen. Axlarna är Amerikanska (Ford 8.8-klump, Lincoln axlar). Jänkelandet har ju ”viss” fokus på stela bakaxlar, varför utbudet av delar till 90-tals delade bakvagnar är… obefintligt.
Mer raljerande kring obefintliga reservdelar och svart bälte i Google kommer inom några veckor. Det här är inte sista posten om drivaxlarna, tyvärr.
Catchtank
Tanken, en 100L-ATL cell, är visserligen fylld med skum så skvalprisken är minimerad och sitter monterad i bakluckan. Men det hindrar mig inte från att använda en catch-tank ändå. Vanligtvis brukar dessa monteras utanför tanken, tex i bakluckan. Tillsammans med pumpar, bränslefilter och ett gäng slangar mellan dessa bildar det en fin prylsallad som är i vägen för allt och effektivt hindrar bagaget från att användas av annat.
Eftersom jag är förtjust i genomtänkta lösningar satsar jag alltså på något annat… Pumpar och catchtank monteras internt i bränsletanken istället. Det minimerar läckagerisken utanför tanken och Smartwire-elgrunkan som visades för någon vecka sedan får hålla koll på strömförbrukningen till pumparna och varna om denna ändras (dvs om de håller på att gå sönder).
Ovan; För den som inte kommer ihåg, så ser tanken ut så här. Alulådan har byggts runt om den för att skydda den från stenskott. Tanken (ba-dum-dish!) är att byta ut topplattan (blå på bilden) mot en ny. Bygga extern påfyllning så man slipper blaska med bränsle i bagaget och få till en bra lösning på catchtank.
Nedan; I samband med att det byggdes ytterlåda så tillverkades även en catchtank. 4L volym, plats för tre bränslepumpar totalt (två huvudpumpar och en förpump). Förpumpen sitter till höger och man kan ana inloppet till catchanken på högra bilden.
Nedan; Det löper sedan i ett rör internt i catchtanken och mynnar ut i tangentens riktning längs den svepta ytan för att inte skapa för mycket oroligheter inuti tanken. Överflödet av bränsle rinner sedan över kanten på catchtanken och tillbaka i den stora tanken.
Nedan; Två huvudpumpar är overkill för nuvarande applikation, men man vet ju aldrig när habegäret efter 7,5L dubbelturbo-V8 blir för stort och då kan det vara bra att vara förberedd med ett extra fäste.
Växellådsbalk
Original växellådsbalk löper mellan subframebenen, dvs den är dryga metern bred och alltid ett helvete att få ner eftersom den sitter ovanpå rambenen och därmed måste snedställas. Men det går inte eftersom det sitter en växellåda i vägen…
Tidigt i projektet konstaterades det att det löper en tvärgående balk i karossen som kunde agera del av en ny växellådsbalk. Genom att nyttja denna, kunde den nya växellådsbalken göras kortare. Ca 25cm istället för 1,4 meter(!), vilket inte bara sparar vikt, utan även värdefullt utrymme för avgassystemet.
En liten fin laserskuren byggsats, levererad av hovleverantören (stort tack!), som kompletterades med två rörstumpar resulterade i en balk som väger drygt 2kg (original landade runt 8kg).
Ovan; Inspiration om att man kunde göra så här kom från någon bild från Speedhunters på en bil jag inte kommer ihåg vilken den var. Med motorn på plats byggdes en enkel mockup som sen mättes upp i CADen för att kunna skära till något snyggare.
Nedan; Balken i karossen hamnar på perfekt avstånd för att agera växellådsbalk. Hål kapades för att hysa infästningar, som självklart svetsades dit monterade i en fixtur för att det skulle hamna 100% rätt.
Ovan; Färdigsvetsad balk. Liten avvikelse fick göras för att optimera utrymmet för avgassystemet – Hela motorpaketet är flyttat ca 30mm åt passagerarsidan vilket plötsligt gjorde att förarsidan hade hur gott om plats som helst för avgassystem, medans passagerarsidan inte hade något. Det löstes genom att helt enkelt fasa den (det är alltså gjort på bilden…).
Nedan; Monterat och klart. 8.8-skruvarna skall bytas mot 12.9 med tiden. De fästelement som finns att köpa i järnhandeln är rätt tråkiga så planen är att köpa ett par kilon från lämpliga donatorbilar på närmaste bilskrot.
P-broms… Det går bra nu…
För den som tror att det bara är att ”bygga ihop” en bil med egna komponenter är det ganska fel. CAD, misslyckade försök, ny CAD, misslyckat… Ny CAD, prov i verkligheten, tillbaka till CAD osv. Tålamodsprövande det här med att bygga bil.
P-bromsen är inget undantag. Den fick aldrig riktigt vara med på ritbordet utan vilket egentligen aldrig var meningen. Det bara blev så. Sånt får man sota för i efterhand genom extra arbete och anpassningar. Bilderna visar bara ett första misslyckat försök. Grundtanken var att försöka belysa att det ofta ligger väldigt många försök bakom egenutvecklade prylar, men kameran fick inte riktigt alltid följa med på alla försöken… Misslyckat försök att försöka visa misslyckade försök med andra ord.
Ovan; Försök 1 blev någon form av skruv i befintligt fäste på spindeln. Ganska lagom placering på hålet i förhållande till var armen på oket hamnar. Dock känns konstruktionen något klen och vajerdragningen efter spindeln och längs karossen är fortfarande ganska oviss.
Nedan; Dock blev i alla fall vajerdragningen från infästning och upp till ok väldigt bra. Kylkanalen till bromsskivan fick bändas lite i sidled. Bromsvajrar är faktiskt original till bilmodellen (trummor med andra ord). Fjädern på vajern är för trummorna. Jag har låtit den sitta kvar, då längden var förbluffande lagom och den faktiskt tvingar tillbaka bromsarmen vilket gör att… Ja, det känns bara bra helt enkelt.
Nedan; Försök två blev egentligen en vidareutveckling av försök 1. En platta som sprider kraften på två skruvar, samt lite justering på infästningen för att inte vajern ska krocka med dedionen.
Högra bilden visar den fantastiska anledningen till att om man ska rita prylar i CAD, ska man rita allt. Även fästelement. Oket kunde placerats 10mm längre bakåt egentligen, men nu hamnade det där det hamnade. Lagom mycket i vägen för att vara för lite i vägen för att egentligen orka bry sig. En fil löste biffen även om det är principiellt fel.
Nedan; Monterat på bilen känns det ju såklart väldigt bra. Till och med vajern visar sig gå att leda någorlunda bra fram till originalpedalen.
Ovan; Så var det bara wiren som skulle dras också!
I en optimal värd hade allt byggs klart innan någon ytbehandling gjorts (karossen skulle alltså inte varit lackad än) och då skulle man såklart bara svetsat fast ett sådant här fäste istället. Nu fick det skruvas i karossen istället. Försänkt skruv på undersidan för att… öh, minska luftmotståndet eller nåt.
Nedan; Handbromswire infäst. Dragningen visade sig bli riktigt bra. I detta fallet ren tur snarare än framförhållning då P-bromslösningen som sagt gjorts efter allt annat varit färdigkonstruerat och tillverkat. En slangklämma håller fast wirehöljet för att avlasta infästningen lite och spara wirehöljet från knäckning eller liknande.
Även en drivaxel-mock kan skymtas på bilen. Mer om det senare…
Torrsumpstråg III
Bara utloppen kvar att få till på tråget innan det kan svetsas ihop. För att vinna lite plats under motorn och slippa klumpiga filter, har istället finmaskigt nät monterats inuti tråget. Om motorn skulle rasa räddar detta förhoppningsvis torrsumpspumpen… vilket visserligen är en ganska klen tröst i sammanhanget, men plånboken kommer vara tacksam.
Ytterplåten sicklades lite mönster i. Egentligen ingen prestandaförbättring, utan rent kosmetiskt. Tråget ser plötsligt lite mer ”köpt” ut nu än tidigare.
Ovan; För att förhindra ett torrsumpspumpsras i samband med ett motorras, har överfallsplåtar och rostfritt nät installerats i tråget. Själva nätet är i princip omöjligt att fästa i något. För att inte riskera att det lossnade, gjordes små överfallsplåtar som helt enkelt svetsades fast mot tråget och som klämde fast nätet. Innan näten installerades, svetsades utsugen på plats. Nedan; Färdiga utsug, sett från insidan. Även ytterplåten har fått sig ett litet kosmetiskt lyft genom några sicklade spår i plåten.
Med allt klart, var det bara det ”lilla” momentet kvar att lägga 2,1m svets på tråget utan att det slår sig… Egentligen är risken ganska liten, men det finns alltid lite nervositet i bakhuvudet med tanke på allt arbete som lagts hittills på tråget. Risken är liten eftersom det sitter monterat mot ett rejält gjutjärnsblock som är någorlunda bra på att ta upp värmen från svetsningen så där blir inte särskilt stora temperaturskillnader. Allting punktades med ca 3cm mellanrum, och därefter lades 3cm långa svetsar i lugnt tempo. Lagom terapiarbete en kväll med andra ord.
Ovan: I lugnt tempo svetsades hela tråget monterat mot motorblocket. Relativt tacksamt arbete med vettig arbetsställning, inte särskilt mycket trånga vrår och lagom gods för att lägga snygga svetsar. Nedan; Det färdiga resultatet blev över förväntan. Tråget slog sig ingenting och TIG-svets ser alltid trevligare ut än MIG-svets. Kvar är att MIGa fast nätet lite bättre på insidan innan tråget kan målas.
Torrsumpstråg ll
För att fånga så mycket olja som möjligt som yr runt i vevhuset, bör utrymmet kring veven vara så litet som möjligt. På förarsidan av motorn är detta redan väldigt tight eftersom tråget är format utefter vevens projicerade perimeter. På passagerarsidan öppnar det dock upp (eftersom oljan skall rinna hitåt), och därmed behövs någon som fångar oljan som slungas från vevaxeln. Detta löstes genom en skrapa som ligger några millimeter från vevaxeln och tar mycket av den oljan som slungas tillbaka upp i vevhuset. För att ta resten, och snabbt få ner det på botten av tråget, sattes ett nät i samma radie som höljet på förarsidan. Nät är nog fel benämning, hålad plåt passar bättre.
Ovan: Yttre konturen av oljetråget kan anas på bilden. För att fånga så mycket olja som möjligt från veven och vevhuset sattes en perforerad (nedan) plåt på evakueringssidan av tråget (den skall svetsas lite mer, men från insidan istället för utsidan).
Ovan och nedan; Säg en konstruktion som inte innehåller kompromisser… Även oljetråg har sådana, i detta fall fick området kring kamdrivningen pysslas om lite extra. 9 kantningar samt ett tak svetsades samman till en enda detalj innan den svetsades mot tråget (för att minska risken att tråget slår sig).
Ovan; Genombränningen kan man inte klaga på. Bilden tagen från insidan…
Evakuering av oljan gjordes i botten av tråget. Istället för att tillverka en lång ränna, gjordes tre separata utsug. Egentligen skulle man haft en 5-stegspump (1 tryck, 4 sug) som de stora grabbarna i nascar osv har. Då hade man kunnat suga från varje kammare. Eftersom tråget är i stål, är det dock lätt att uppgradera om en fetare pump skulle införskaffas i framtiden.
Istället suger mittenutsuget 50/50 från de två mittersta kamrarna. De yttre suger ca 25/75 inner-/ytterkamrar. Den totala utsugsarean från varje kammare är alltså lika stor.
Ovan; För att få en snäll båge på rören och uppnå tillräcklig längd för att ens kunna hantera ledningarna lades utloppen på motsatt sida från pumpen. Alternativet hade varit att vända dem 180º, men då hade ledningarna blivit mellan 3 och 12cm. Lite pilligt… AN10-storlek valdes på dem. Normalt är AN12, men det blir ganska klumpligt och 3st AN10 utlopp suger lätt ut mer olja än 1st AN12 klarar att pumpa in…
Nedan; För att ändå maximera utsugsvolymen användes rör istället för slang. Rören är tunnväggigare än slangarna, vilket gör att man klarar sig med en AN10-koppling (lite specialbyggd…) och ändå nästan kan ha samma volym som AN12. Endast sista centimetrarna mellan pump och rör blir slang för att kunna ta upp visst flex. Lite luddigt förklarat kanske, men jag vet vad jag gör… 🙂
Högra bilden: Nä, men titta. Vilken ”tur” att utsugen passar så bra mellan rambalkarna att motorn kan sänkas ner (ytterligare 60mm – redan 80mm sänkt) utan att ta i ramen. Med tanke på att placeringen av utsugen i tråget är låst, är det nästan som att någon har tänkt på detta när ramen ritades… Suget efter en växellåda med bättre markfrigång blir bara större och större…
Ovan och nedan; Bygge av utsug. Det är inte många droppar olja som stannar kvar i tråget – utsugen hamnar bara någon millimeter från botten av tråget.
Vanliga JIC10/AN10-kopplingar från en hydraulfirma har svarvats om. Nedre högra bilden visar hålet som blivit koniskt uppsvarvat. 10º resuterade i rätt rejäl ökning i diameter.
Övre länkarmar
Precis som nedre länkarmen, fick även övre (såklart) byggas från scratch. Det är mer pill än vad man tror, men slutresultatet blir bra.
- Kapa upp material och notcha rören
- Svarva hylsor till bussningarna
- svarva axlar till bussningarna eftersom original var för korta för min applikation
- plåtar till infästning för spindelled
- Inpassning mellan rör och plåt vid spindelled
- I med det i en fixtur och sätt några svetsloppor
- Ur med det ur fixturen och provmontera på bilen
- Testa alla maxlägen för att kontrollera att inget tar i
- I med det i fixturen och helsvetsa allting
Som sagt, det blir många timmar… Bra med stabil fixtur inför framtida reservdelar dock.
Nedan; Monterat på bilen. Det blir bara punktat tills att måtten kontrollerats och allt stämmer. Lite förstärkningar är kvar att fixa på armarna, men det blir som sagt vid slutgiltig svetsning…
PLÖTSLIGT är framvagnen nästan komplett! Spindeln sitter där och egentligen saknas bara pushrod och lite finlir med lagringen av vipparmen innan framhjulen kan hängas på för första gången!
Nedre länkarmar
Det börjar som ett litet plockepinn. Alla standarddetaljer – länkhuvuden, spindelleder, bussningar, skruvar etc – köps hem. Därefter svarvas hylsor till bussningar, rör kapas i rätta vinklar och gängade hylsor till länkhuvuden svarvas. Plåt skärs och kantas.
Därefter är det das att tillverka en stabil fixtur – länkarmar är, och ska vara, förbrukningsvara. På så sätt slipper man förhoppningsvis reparera saker på ramen vid en eventuell smäll. I detta fall fungerar fixturen både till övre och undre länkarmar.
Notera att rören är plattovala, 40x20mm. I ärlighetens namn är det för att det ser coolt ut. Det här är en karossbil, så någon aerodynamisk fördel ger de knappast. Dock borde de vara något styvare än 30mm runda rör vid retardation. Eftersom pushrod-infästningen sitter långt ut på armen, påverkas inte själva armen nämnvärt av fjädrandet. Planen var från början att ha pushroden monterad direkt i spindeln, något man ofta ser på formelbilar. Fördelar är bl.a. att det avlastar spindelleder, länkarmar kan göras lättare mm. Tyvärr är det svårt på gatbilar pga det större styrutslaget (+-35° jämfört med gissningsvis +-15)
Infästning för kylarram
Det mesta är klart på framvagnen nu. Så även infästningar för kylarramen. Kylarram, samt kraschboxar är tänkta att skruvas i mot delarna på bilden. Om det går att få till två vettiga kraschboxar återstår att se – inget är CADat än, men allting går ju…
Nedan; Infästningarna jiggades (såklart!) får att förhållandet mellan dem skulle vara exakt. Därefter är det enkelt att rita upp en vettig kylarram.
Subframe, igen
Veckans jobb på framvagnen. Det mesta börjar bli färdigt nu.
Ovan; Anpassningar till befintlig ram kräver lite extra detaljer här och där. Gamla urtaget för styrväxeln har delvis fått läggas igen. Som om det skulle användas igen… Högra bilden visar att det faktiskt börjar bli klart – vipparmsinfästning och fästen för övre länkarmar.
Nedan; Vipparmsinfästningarna har svetsats både från in- och utsidan. Rejäl V-fog på utsidan och lika-bra-att-svetsa-här-också-fog från insidan.
Nedan; Även rambenen är numera svetsade som de ska.
Bara interfacet mot framtida kylarram kvar, sen är det dags för grundfärg!
Svetsning…
Det blir tämligen många meter svets när man håller på med plåtkonstruktioner… Vill inte riktigt räkna efter hur mycket det rör sig om, men det har uppskattningsvis tre 50-liters TIGtuber på att bygga fram och bakvagn och ett antal timmar. Bara ”de sista detaljerna” på subframen som pågår just nu har hittills tagit ca 100h att färdigställa. En grov uppskattning säger att byggtiden på subframen är runt 200h. Lägg därtill konstruktionstid i datorn också…
Ovan; Fixturen positionerar både länkarmsinfästningar och vipparmsmontage. Det är väl inte positionering på tiondelen med tanke på att det är vanliga fyrkantsprofiler, men det håller betydligt högre toleranser än vanliga biltillverkare gör på sina saker.
Nedan; Hade nästan vant mig vid att se ramen utan infästningar…