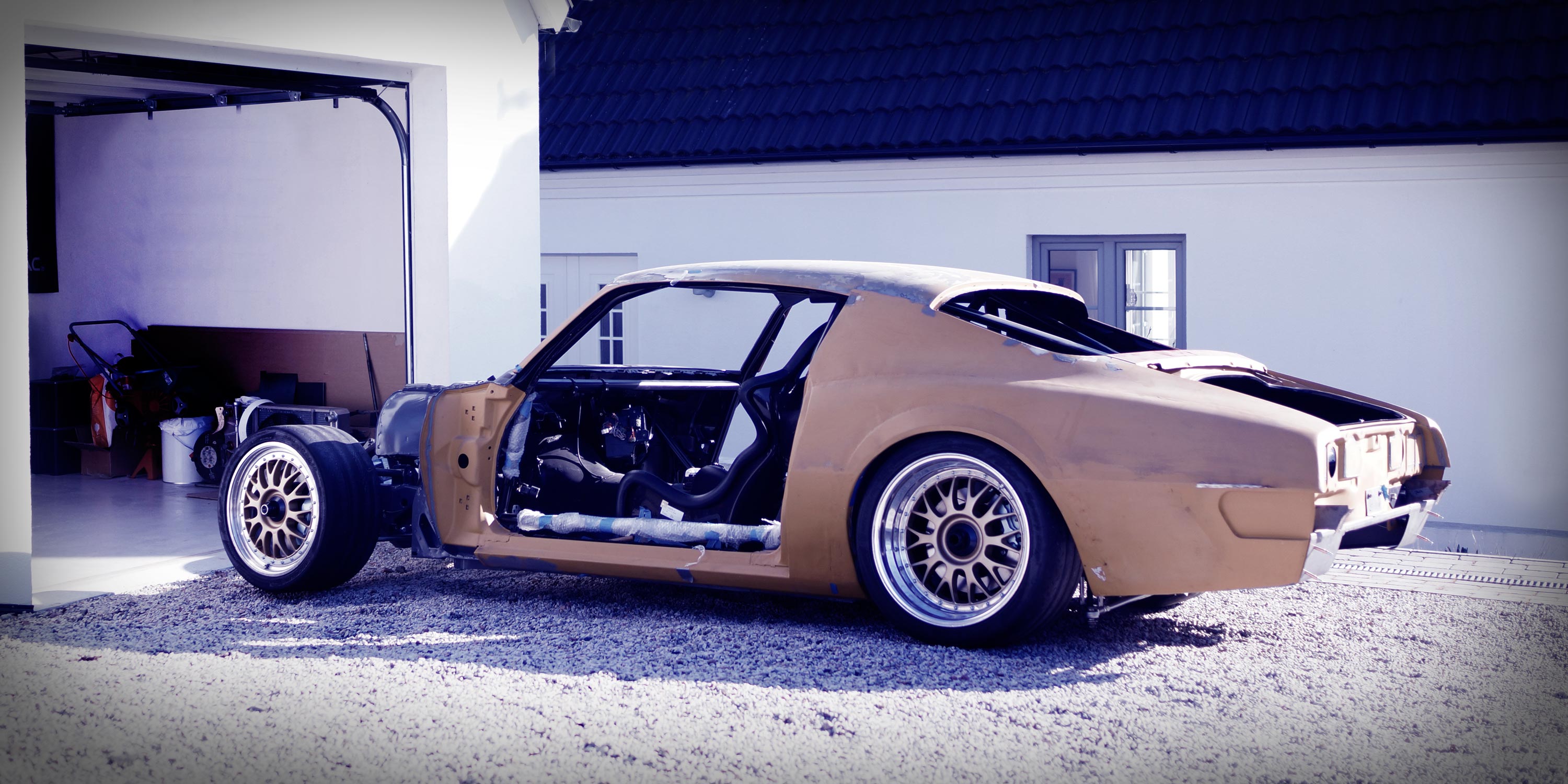
Kategori: Drivetrain
AC-kondensor
Kondensorn är på plats, och funkar inte enbart som AC-pryttel utan även som stenskottsskydd för kylaren… Kanske ett dyrt skydd, men kylaren är ju ännu dyrare! Skämt o sido, det blir något nät i fronten också för att hålla små barn och fåglar borta i alla fall.
Ovan; Gick visst lite fort i själva byggfasen här så kameran hann aldrig komma fram. I alla fall – blåa ramen sitter skruvad fast i kylarramen (grå). Kondensorn sitter därefter skruvad fast i den blåa ramen. På sikt, när fronten är på plats, kommer en kanal byggas mellan blå ram och front för att all luft som tas in i fronten ska pressas genom kylaren. 1mm aluminium, vikt ca 600 gram.
Nedan; Och där var det klart! Begagnad kondensor från en Volvo 850 visade sig matcha bredden perfekt på C&R-kylaren. Himla trist att hänga dit begagnade delar, men det kändes svårt att motivera nyinköp av en kondensor när man vet att donatorn fungerar. Om ett halvår ser man förhoppningsvis inte den längre när karosspaneler börjar komma på.
Ett halvår? ETT HALVÅR??? Sa jag ett halvår? Ett halvt decennium menade jag såklart, med nuvarande tempo…
Nedan; Svarvade fina skruvar att svetsa fast i ramen till kondensorn. Dessa håller som sagt kondensorn. När man ska svetsa aluminium är det bra att slå över svetsen till AC läget, istället för DC. Kör man på DC kan man värma i en evighet utan att något händer… Till slut smälter man sönder sina fina aluminiumskruvar…
Gör om gör rätt med andra ord. Nya fick svarvas och med AC-läget aktiverat gick det ”något” enklare att få dit dem…
Nedan; Svetsskruvarna ovan är de som kondensorn sitter infäst i. Muttern respektive skruvskallen är de som håller själva kåpan mot kylarramen. När fronten monterats skall det byggas en kanal från luftintaget i fronten som ansluter mot kylaren (rättare sagt kåpan runt kylaren som nu byggts).
Tändspolar 2.0
De skymtade på bild i förra veckan.Tändspolarna har flyttats. igen. För några månader sedan såg det ut så här, men i och med förra veckans förstärkning runt motorn så fick de flyttas.
Ovan; Ja, så här har det sett ut fram tills nu. Vänstra bilden alltså.
Ny placering är inte helt självklart. De är rätt stora, och klumpiga. Två hade gått att gömma undan, som tex i framkant på motorn (vänster). Åtta är omöjligt… Nåväl, efter lite om och men var det dags att veva igång fräsen.
Nedan; Steg 1 är riggat på bilden nedan, en gammal skrotbit som får agera provbit. Hål borrade i stycket för att kunna skruva fast den i fixturen (som utgörs av ytterligare en gammal skrotbit).
Nom-nom-nom-nom. Fräsen tuggar aluminium som aldrig förr.
Nedan; Färdigt moment – då var det dags att…
..vända biten, borra nya hål, montera den i fixturen igen och dra av ytterkanten.
Nedan;
Efter några timmar i fräsen, någon timme vid svarven för att göra en himla massa distanser och lite rostfri gängstång så får man…
Nedan; …finfina tändspolehållare. Kompakt paketering jämfört med tidigare.
Motorattiraljer
Med torrsump på rätt plats i djupled var det dags att få dit AC-kompressor och generator, vilka blir de enda tillbehören. Servot är eldrivet och sitter på rattstången och vattenpumpen är också eldriven, så installationen blir ganska clean.
AC-kompressorn har monterats längst ned pga att den var tyngst.
Ovan; För stunden är plåten som håller generator och kompressor gjord av stål. Numera finns det ju en fräs i garaget, så framtiden får utvisa om lättare komponenter hittar dit. För att få den där riktigt stabila, flexfria infästningen av generatorn sitter den skruvad både i toppen och i plåten. Ultrastabilt var ordet.
AC-kompressorn hamnade under med gott om plats till grenrör och framvagnsbalk. Lite trist med begagnad kompressor när allt annat är nytt, men den får väl putsas upp lite i framtiden.
Nedan; Även kompressorn sitter riktigt stabilt tack vare att den är skruvad i blocket. Lite svårt att ta foto på, men CAD-bilden till höger borde förklara principen, även om alla plåtbitarna inte riktigt finns där. Skönt att den där bränslepumpsblockeringsplattan för 40 dollar med risigt fräst fågel syns så extremt mycket. Kommer sticka en direkt i ögonen när man sticker in huvudet innanför framhjulet…
Ovan; Sådärja! Det blev väl inte så pjåkigt, och framför allt relativt kompakt!
Tänkte börja med förenklad remdragning, dvs att inte använda det extra löphjulet. Om det visar sig att remmen slirar på generator eller AC-kompressor finns möjligheten att fixa längre rem och dra den via löphjulet. Att spänna remmen görs med hjälp av klassiskt långhål för generatorn (nedersta skruven på högra bilden)
Nedan; Jo, men det blir ju rätt bra. Skulle vilja haft generatorn lite längre in mot centrum, men då tar pluspolen från baksidan i topplocket och det är typiskt dåligt. Normalt sett sitter komponenterna ca 7-8cm längre fram på motorn. För att inte ha en torrsumpspump som sitter ännu längre fram än så och vinglar, flyttades allt tillbaka så långt det bara gick. Det ger dessutom en hyfsat kompakt motor.
bufk
remskiva
Även ny remskiva har tillverkats. Dels för att konvertera till multirib, men även för att all kringutrustning har flyttats närmare motorblocket (längsled) för att få en kompaktare installation. Även torrsumpsdriften har integrerats för att på så sätt spara vikt.
En styrd fräs visar sig vara garagets nya Swiss Army knife – den kan tillverka det mesta utan några större problem.
Ovan: Råämnet har snidats fram i manuell svarv fram innan fräsen blev färdig. Bearbetningen på bild hade så klart gått att göra i manuell svarv också, men den hade tagit mer än 15 min som den gjorde i fräsen…
Den koniska ytan är 3D fräst med 0,2mm stigning och en 8mm fullradiefräs. Blev faktiskt riktigt bra. Lite läskigt att experimentera på sådana här bitar (hade aldrig gjort 3D-program tidigare), men fega pojkar får inte pussa vackra flickor. Och inte köra coola bilar heller för den delen.
Nedan; När man har egen fräs har man plötsligt råd att lägga tid på detaljerna som inte syns – insidan har fått lite lättning, samt konisk urfräsning i botten som är parallell med utsidan. Sparade flera gram.
Ovan; färdigt resultat. 890 gram (första bilden) slutade på 360-nånting gram i slutändan. Ganska najs att ”sparat” ett halvkilo.
Nedan; Bröstkåpa och svängningsdämpare monterad. Även 60-2 hjulet för vevaxelsignal till sprutet är på plats. Notera lättningshålen – tidigare 60-2-skiva var homogen.
Ovan; Blev ungefär hur bra som helst! En skyddskåpa över remmen hade varit fint, och dessutom gett lite mer OEM-look på det. Dock inte denna gång. Det ska finnas någonting att pyssla med i framtiden också…
Med färdig remskiva kan äntligen slutgiltiga installationsmått på torrsump, AC-kompressor och generator äntligen bestämmas.
kamaxelgivare & bröstkåpa
Eftersom nya sprutet är lite mer sofistikerat än det gamla hedenhös-Electromotive som satt där tidigare, finns möjligheten att köra sekventiell insprutning. För att kunna det, behövdes en givare på kamaxeln. Inte helt trivialt att komma åt kamaxeln någonstans – fördelaren är sedan länge borta. Efter lite om och men konstaterades det dock att bröstkåpan framför kamaxeldrevet var bästa stället. Eller det minst dåliga i alla fall. Rätt mycket pyssel med att få dit en dock, vilket borde avspeglas i alla momenten nedan…
Ovan; Kamaxeldrivning och lämplig indikeringspunkt behövde ordnas för givaren
Nedan; Sagt och gjort – Väck med drevet, upp med det i fräsen och koordinatborra ett M6-hål. Två faktiskt – blev lite osäker på om hjulet var balanserat och man därmed skulle behöva montera en motvikt på andra sidan av hjulet. Under arbetets gång blev det dock ganska uppenbart att 19 grams extravikt på ena sidan knappast skulle bli ett problem.
Nedan; Indikeringspunkt tillverkad. Man kan använda en skruvskalle också, men jag ville ha så mycket material som möjligt för att få säker avläsning. Därmed blev det hockeypuck med stoppskruv och några små låsningar med TIG:en. Skruven sattes sedan med Loctite 270 som tål över 150 grader samt är oljeresistent.
Ovan och nedan; Sen var det dags för att ge sig på bröstkåpan. Friskt fräst och hälften vunnet, som man brukar säga…
Skrev ut ett antal fullskalamallar för att hitta lämplig position. Därefter körnslag i kåpan som får utgöra nolla vid fräsning. Hålet gick skrämmande snabbt att ta upp och sen fanns det ingen återvändo…
Ovan; När kåpan var fräst, var det bara att sätta igång med själva fästet för givaren. Rigga om fräsen, tillverka ny bit. Även denna med hål för att kunna nolla in fräsen inför slutgiltig bearbetning.
Nedan; Därefter över med bitarna till svetsen för att lappa ihop dem. Grundtanken var att svetsa från insidan för att behålla en snygg utsida. Tyvärr sprack det pga svårigheter att komma åt i dalen (som blir förhöjningen i ovankant på bilden), så den fick svetsas från utsidan också…
Nedan; Färdigsvetsad kåpa fick därefter en slutgiltig bearbetning i fräsen. Ville inte göra denna förrän efter svetsning pga det tunna godset. Resultatet blev ju dock ganska tjusigt. Givaren passade till och med!
Även höjdled (som är rätt känsligt) stämde så när som på någon hundradel.
Nedan; Färdigbearbetad och svetsad detalj. Nya anslutningar för vatten, eftersom någon tomte (undertecknad…) gav sig på dessa i förra motorbygget för ca 10 år sedan. Inloppet blev större än tidigare eftersom nya kylaren använder större slanganslutning.
Aluminiumet är 40 år gammalt gjutgods och har sett sina bättre dagar. Med andra ord målades det i… gjutjärnsgrått (!) för att matcha motorblocket.
Ovan; Pricken över i:et; en Firebird-block-off-mekanisk-bränslepumps-plåt. Köpt för 350:- för tio år sedan. Repig, sned fågellogga, för stor fågellogga som täcks av skruvskallarna samt en ytterkontur som inte stämmer med bröstkåpan över huvud taget. Samma land som kom på och utvecklade iPhone tillverkar alltså denna pryl… Högt och lågt. Nåja, den fyller sitt jobb i alla fall. Med tiden kanske det blir en egen, som såklart är urfräst på baksidan för att spara vikt.
Kylarram pt. lll
Kylarramen är klar och kylaren är på plats! Kylaren är en, något överdimensionerad, modell med integrerad värmeväxlare för motoroljan. Lär inte bli några problem med för varm motor förhoppningsvis.
Ovan; En lätt begagnad kylare från en nån tävlingsbil (från nåt Penske-team) köptes för många år sedan från eBay.
Nedan; AN20 anslutning på inloppet, 50mm utlopp. Lär inte bli några problem att flöda vatten till motorn… Utöver det finns där fyra andra uttag på kylaren som kan användas till givare eller annat.
AN16 på motoroljan – samma sak där med flödet.
Ovan; Översta profilen till kylaren. Samma sak som undre – ett antal omtag och rätt mycket fräsning. Höll på att få hybris och fräsa in ”Firebird” istället, men fick det aldrig att se bra ut och konstaterade snabbt att ett ingenjörigt fackverk är betydligt stilrenare.
Nedan; Svetsat och klart. Drygt fyra kilo väger ramen och trots blygsam vikt blev den helt jävla extremt bautastyv! Eftersom skärmarna skall fästas mot kylarramen är det bra – inget karossfladder i onödan.
Ovan; Ja, här skymtar visst lite framtida uppdateringar också, men försök fokusera på kylarramen så kommer de andra sakerna om inte allt för många veckor. Kylarram med kylare i… Kvar att tillverka är anslutningen för ventilationskanalen från fronten – tanken är att det skall vara tätt så att all luft som tas in i fronten passerar genom kylaren. Fästen för AC-kondensorn är också kvar att ordna. Ja, du läste rätt – det blir AC… Någon komfort måste man få ha.
Nedan; Framåtlutad kylare ger bra åtkomst för att tex byta kamaxel utan att plocka ur motorn. Det är en bra egenskap.
Nu får kylsystemet mogna lite. Några andra punkter behöver färdigställas innan de sista detaljerna i kylsystemet ordnas.
Bränsletank på plats
Tank på plats, för första gången. Har medvetet väntat med att ta hål i karossen för tanklocket av den anledningen att se till att fallhöjden på röret blir tillräckligt högt.
Nedan; Man ser på bilden att tanken sitter något till höger. Dels för viktfördelningen, men även för att lämna något bagageutrymme kvar. Som det nu är får man inte bara plats med VISA-kortet, utan även tandborste och en plastpåse med lämpligt innehåll. En riktig GT-vagn med andra ord…
Nedan; Men va falls? Tanken kommer ju högre upp än beräknat! Idén att placera tanklocket på förarsidans bakskärm verkar skita sig och det är inte bra. Hur ska man nu kunna ha 60-tals gentlemannaräserstuk på ekipaget?
Som syns på högra bilden så är det svårt att få vettigt fall från tanklocket till bränsletanken. Lite utrymme behövs för att sticka in pumpmunstycket i tanklocket, och dessutom behövs lite utrymme ovanför tanken för att få plats med en krök.
Ovan; Dags att tänka om vad gäller designen. Så här var ju grundidén, att tanklocket skulle sticka upp lite genom bakskärmen likt systerbilen ovan. Jag är inte ett jättestort fan av att placera det på bakluckan, men det kanske ändå får sluta så?
Nedan; Det finns ju några andra biltillverkare som har monterat det på bakluckan och det ser ju inte helt dumt ut faktiskt. Pontiacen är visserligen inte riktigt lika kurvig över rumpan som Ferrarin och Jaguaren nedan, men det kanske inte ser dumt ut ändå. Får nog fundera lite på saken…
Kardanaxel
Kardanaxel blir, som allt annat, speciallängd för att passa med den tillbakaflyttade motorn. För många år sedan införskaffades en Ford Motorsport 3″ aluminiumkardan. Den verkar hålla för de flesta Fordägarna (Fordägare brukar ha fullt upp med att få resten av bilen att hålla, så de kanske inte märker att kardanen också går sönder…) och med tanke på att Pontiacen blir så lätt att ankare behövs när den skall parkeras, känns det som den kommer leva ett ganska bra liv i Pontiacen.
Längden var ju så klart fel, och att få tag på någon i Sverige som kunde tänka sig att korta en aluminiumkardan visade sig vara svårare. Balansering gick att lokalisera dock, men då behövde den vara färdigkortad innan.
En utmärkt anledning att införskaffa en AC/DC-TIG för att kunna göra jobbet själv med andra ord. Kortningen blir ju ganska dyr om man tar med svetsen i kalkylen, så det får man helt enkelt låta bli att göra. En AC/DC maskin är ju dock något som är väldigt bra att ha, och nu när man äntligen hittat en anledning att köpa en gäller det att passa på. Blir nog inte sista aluminiumprylarna på Pontiacen…
Ovan: Patienten på (det kliniskt rena) operationsbordet. 137mm skall kortas, men det behöver planeras lite eftersom änden för knutkorset inte går att spänna upp i svarven.
Nedan; Änden uppspänd i svarven. Den får svarvas rätt från början (en tolk tillverkades för att hitta rätt diameter för röret) eftersom chucken håller på de sista millimetrarna (som får stickas av innan den plockas ur). Inget vidare enkelt att spänna upp den – Ford verkar slarvat från början, så hela änden kastade drygt en millimeter (men sånt verkar man glatt balansera bort i serieproduktion). Efter ganska mycket om och men satt den dock rätt i svarven.
Ovan; Hmmm, det är något som saknas på den här kardanen…
Den gör sig helt enkelt bättre som polerad!
Nedan; Omsvetsningen närmast diffklumpen – jag antar att Ford är bättre på att svetsa än mig, och då är sannolikheten störst att den går sönder i den nya svetsen. Går den sönder, är det bra om det inte blir ett spett ner i asfalten som sliter loss hela bakvagnsinfästningen. Har inte gjort något fäste för det, men gissningsvis kompletteras axeln med en fångring i framtiden, även om det känns lite dragracingvarning på den…
Nedan; Same but different, som kinesen hade sagt! Kortad, polerad och balanserad! Visade sig att det var obalans i båda ändar (skäms, Ford!) men det fixade Göteborgs Kardanaxelservice till. Visade sig vara ganska få som ville balansera aluaxlar (eftersom alla svetsar på stålvikter), men ovan nämnda företag verkar ha gjort ett väldigt bra jobb.
Dekaltrimning, ja… Hmm. De två svarta parallella strecken är för att upptäcka om materialet vrider sig med tiden (dvs om axeln är på väg att bli utmattad). Texten tillkom av bara farten. Kardanaxeln döljs effektivt bakom avgassystemet, så knappt ens besiktningsmannen kommer kunna se den…
Tändspolar
Eftersom det blir nytt styrsystem/ECU (DTA S80 PRO) fick även nya tändspolar lokaliseras. Valet föll på GMs LSx-spolar. Tämligen poppis, robusta och asbilliga. När det handlas specialprylar i det här projektet köps det alltid hem lite extra, tex dubbla uppsättningar bromsskivor för att kunna ha ett par på hyllan. Typ 10 uppsättningar belägg, nio tändspolar, tre torrsumpsremmar, ett antal topplockspackningar osv. Bra att ha saker på hyllan om man skulle köra sönder.
Ovan; GMs LSx-spolar. Har bråkat en hel del med att försöka hitta ett vettigt ställe att montera dem på. Flertalet ställen har testats, och för närvarande leder placeringen ovanpå ventilkåporna. Inte snyggaste installationen, men alla ingenjörer vet att funktion går före form…
Lite laserskuren aluminium trillade hem för att underlätta montering.
Nedan; Monterar spolar i godan ro när man plötsligt inser att potatisälskande Bob på monteringslinan i Idaho, eller var den nu kan tänkas ligga, inte har haft en bra dag när han byggde mina spolar. Tittar man på högra spolen som är monterad mot aluplåten, inser man att fästena inte sitter i linje med varandra. Skiten har hamnat snett vid montering och därefter gjutits in i epoxi. Inte mycket att göra åt – inget man kan plocka isär och korrigera direkt. Tur att man köpte nio med andra ord…
Nedan; Jaha, så här blev det. Man äger alltså en Ontiac numera. Det var ju kanske lite snopet, även om en bokstav mindre inte är hela världen. Eller ärlden…
Hmmm, år og uga å en ite ill…
Catchtank
Catchtanken är i det närmaste klar. Kvar är att lösa ledning av påfyllningsröret och var tanklocket skall placeras, men det tar nog ett tag att klura ut (eller tills att det blir prioriterat i alla fall). För övrigt känns det väldigt bra att lyckats klämma in pumparna inuti tanken istället för att ha ett virrvarr av rör i bagageutrymmet. Pumparna sitter bättre skyddade, mindre buller, minskad risk för läckage och säkert någon fördel till.
Bränsletanken känns så säker den kan bli. Lite trist att åka omkring med 100L bensin om något skulle hända, men säkerheten är prioriterad så gott som det går; Plasttank med invändig gummiblåsa. Skum i tanken, främst för minimerad lastförskjutning men det rinner lite saktare ur tanken om det ändå skulle gå hål. De flesta komponenterna inuti tanken gör att volymen bränsle i ledningar utanför tanken kan hållas nere, samt kulor som stänger tanken om man skulle råka lägga bilen på taket.
Nedan; Blev faktiskt rätt fint i slutändan. Nivågivaren (röret till vänster) är visserligen för kort – längre modell var av en annan typ och kostade orimligt mycket pengar. Det får duga tills vidare, och istället bli ett uppgraderingsprojekt i framtiden. På bilden syns också förra veckans första CNC-frästa detalj – röret för att hålla kulan som stänger om man hamnar på taket.
Nedan; Livet blir enklare med en styrd fräs. 🙂
Alla hålen i plattan nedan kördes fram med fräsen. Röret på högra bilden känns säkert igen från förra veckan. Den är tänkt att hysa kulan, som landar mot det svarvade sätet om olyckan skulle vara framme och bilen bestämmer sig för att lägga sig på taket. Hålet för bränslegivaren (stort hål med fem små runt om) – ATL tog i och gjorde ett asymmetriskt bultmönster, men bara så lite att man inte märker det. Upptäckte det i sista stund och lyckades googla fram håldelningen.
Ovan; Så här då alltså… I hålet till vänster på bilden hamnar avluftningen. Samma funktion, dock köpt istället. Andra bilden visar genomföringarna till tanken. AN8 (1/2″ rör). Den lilla kopplingen kommer bli genomföring för elen.
Nedan; Tryck och returkopplingar. Fullradie för trycksidan för att maximera flödet (jo, här klyver vi hårstrån, jag vet…), och vanlig för andra sidan. Kunde såklart valt fullflöde på båda, men nu blev det som det blev. Tredje genomföringen blev lite hemmapyssel. Kontakt för bränslepumparna. Fylls med epoxi när det är tid för det.
Ovan; 3D-printat bränslefilterfäste, generation1 och generation2. Ettan var tänkt att nitas i plåten på bagagerumsgolvet. Efter utskrift, låg det och skräpade i garaget ett par månader i väntan på att bli prioriterat. När det var dags, kom det nya insikter och istället gjordes en variant som nyttjar befintliga hål för infästning av bränsletanken.
3D-printers erbjuder konstruktioner som annars hade varit omöjliga. Hålen man ser på bilden är genomgående och alltså spåret för slangklämman som skymtar nedan.
Kopplingarna borrades upp ytterligare ca 2mm i diameter och har blivit konade i ändarna för att inte strypa så mycket.
Nedan; Filterinsats. Vanligt Volvo V70-bränslefilter – enkelt att köpa på hyllan i Sverige de gångerna det behöver bytas.
Drivaxeldamasker, det löste sig
Fortsätter förra veckans raljerande kring damaskerna och hittar någon sida på nätet som beskriver hur man sticker av flänsarna till diffen och borrar nya mönster för att kunna köra Porscheknutar med Ford 8.8-klump. Jättebra, men det känns lite trist att börja om nu, särskilt eftersom man med porscheaxlarna fortfarande behåller yttre Lincoln-knuten.
Denna och förra veckans post beskriver ett arbete som sker till och från under flera veckor (samt några nätter då sömn hade föredragits istället). Till och från kollas alternativen upp. Flera av alternativen kollas dessutom flera gånger, i hopp om att internet har ändrat sig och blivit snällt. Det har det inte.
Men så kommer snilleblixten, som anses självklar i efterhand, att utöka sökningen kring systerbilar. Inte bara till de som har samma bakvagn, utan till de som använder samma diffklump istället. Vilket även inkluderar bilar som Ford F150, Lincoln Navigator, Ford Explorer och ett helt batteri med andra fordon.
Plötsligt trillar det upp nya sökträffar på eBay, nya affärer som listar komponenter. Gud verkar ha anlänt med damaskåterbäringen som eftersöktes i förra veckan.
Ovan; Plötsligt finns de bara där, på eBay av alla ställen. Hela internet har dammsugits, och nu finns de framför näsan på en. Haschtag Win på den liksom!
En eBay-säljare får förtroendet att leverera damasker efter att ha visat dimensioner som stämmer ganska bra överens med Mark VIII. Visserligen lite små, men gummiprylar brukar vara övertalbara när det gäller töjning. Leveransen tar evigheter känns det som. Två evigheter till och med, men till slut finns de hemma i garaget och skall bara provas.
De passar. Lyckan är obeskrivlig och motivationen når nya toppnivåer!
Ovan och nedan; Montering av drivaxlarna var tämligen rätt fram.
Reservdelsförsörjning – damaskjävlar
Projekt byggda i Europa bör byggas med Europeiska delar. Projekt byggda i Europa bör byggas med Europeiska delar. Projekt byggda i Europa bör byggas med Europeiska delar. Projekt byggda i Europa bör byggas med Europeiska delar. Projekt byggda i Europa bör byggas med Europeiska delar. Projekt byggda i Europa bör byggas med Europeiska delar. Projekt byggda i Europa bör byggas med Europeiska delar. Projekt byggda i Europa bör byggas med Europeiska delar. Projekt byggda i Europa bör byggas med Europeiska delar. Projekt byggda i Europa bör byggas med Europeiska delar. Projekt byggda i Europa bör byggas med Europeiska delar.
Precis.
Den här typen av omfattande projekt har alltid sin beskärda del av motgångar. Det har hittills varit förhållandevis lite, men just drivaxlarna visade sig bjuda upp till en riktig strultango.
Ovan; En av låsringarna sprack när axlarna demonterades. Att få tag på en ny var lättare sagt än gjort eftersom måtten var lite ovanliga. Det hade inte gått, om jag inte gnällt på ett forum där en vänlig läsare gick ut och inventerade sitt garage – hittade två C-ringar i nästan exakt samma dimensioner, tog sig tid att kontakta mig och erbjuda mig dessa, samt lägga sakerna i kuvert, frankera och lägga på lådan. Ett beteende som är lite ovanligt i dagens självupptagna värld. Ett oändligt stort tack skall denne personen ha – helt ovärderlig hjälp!
Tyvärr är dock inte detta den enda motgången…
…”Någon” har nämligen råkat köra en skruvmejsel genom ena damasken vid demontering.
Ingenjörajäveln ska alltså inte bara trumlas i ett bad av svarvspånor och tvagas med rostfri stålborste (från ”länkarmsfadäsen” här om veckan), utan därefter även doppas i begagnat drivaxelfett (alla vet hur det luktar). Man kan såklart rädda klanterier likt denna genom att beställa hem reservdelar och ha på hyllan när det är dags för återmontering, men detta gjordes inte. Antagligen pga det helt enkelt var omöjligt att få tag på reservdelar, i kombination med en slapphänt 80-talist med inställningen ”men ååååh palla, det fixar jag sen liksom”.
Ovan; Det är ett yttepyttelitet hål, här på bild lagat med cyanoakrylat i ett försök att reparera befintliga damasker. Lagningen blev nog bra, och kommer nog att hålla. Men det känns ändå lite risky att förlita sig på dessa. Dessutom behöver reservdelar finnas om/när dessa går sönder så om man låter bli att försöka hitta nya damasker nu, skjuter man bara problemet framför sig.
Men det är ju bara att leta upp lämplig internetshop och köpa en uppsättning nya?
Drivaxeldamasker till Lincoln Mark VIII, som tillverkades mellan 1993 och 1998. Lincoln… Få se nu, Ford lade ner märket vid 2008. Reservdelsförsörjning, från nedlagda märken? Lika troligt som att solcellsdrivna ficklampor eller pedaldrivna rullstolar skulle bli nästa storsäljare.
Efter några timmars googlande börjar insikten om att de faktiskt inte finns som reservdel längre komma, men en del företag verkar fortfarande ha lite gammalt liggandes på hyllorna. Med andra ord inventeras varenda drivaxeldamaskåterförsäljare (hej, Sture Allén) för att se vad som finns. Yttre damask finns lite överallt. Inre lyser med sin frånvaro. Det är så klart inre som är trasig.
Forumanvändare borde ha svar? Lincolnförarna verkar dock inte vara den typen av bilägare som byter damasker för skojs skull. Svaren uteblir och ovissheten är fortfarande komplett.
Det säljs ”refurbished half shafts” i någon form av utbytesprogram, så damasker måste finnas någonstans. Drivaxlarna är ju kortade, så det är knappast lönt att köpa nya kompletta axlar. Timmar och åter timmar på google leder mig fram till en gammal HTML-sida om en kille som byter bakvagn i sin Mustang och skriver om nåt litet företag i innersta USA som hjälpte honom.
Hittar företaget, inser att det är fax som gäller om man ska ha tag på dem då inget telefonnummer eller mailadress finns på hemsidan. Faxar flera gånger utan svar.
Hittar även några andra företag som sysslar med drivaxlar. Ett svarar att ”jajamän, de har minsann damasker på lager – hur många vill jag ha?”. Lyckan är komplett! Prisa Gud, här kommer damaskåterbäringen! Jag tänker att tio stycken är lika bra att köpa, men priset är ganska saftigt. Fortsätter konversationen, dubbelkollar några mått, skickar bilder och allt är ”inga problem”. Varningsklockor ringer – har de koll? Ber om bild tillbaka på produkten de planerar att UPSa till Sverige. Ingenting stämmer, man ser direkt att den inte passar. Konfronterar dem och frågar hur de tänker sig att den skall passa – möts av tystnad. Tillbaka på noll. Prisa inte Gud. Förbannade drivaxeltillverkare, utsända av Satan själv för att försvåra för entusiaster.
Ovan; Drivaxeldamaskjävlar. Två stycken.
Tillbaka till internet då. Dags att börja leta gemensamma bilmodeller där samma bakvagn funnits. Lincoln MKVIII, Ford Mustang SVT Cobra (specialmodell med individuell bakvagn), Ford Thunderbird och någon Oldsmobile. Mustangen har större drivaxlar, så de damaskerna passar inte. De andra tillverkas det inte heller några damasker till längre.
Någonstans i misären önskar man sig att man hade europeiska delar. Även om de inte fanns längre, hade det varit enklare att traska in på Biltema och hitta något som låg nära i dimensionerna. De stora reservdelsnasarna har inte mycket amerikanardelar på hyllorna och tyvärr skiljer sig det en del kring kulturen olika bilbyggarkontinenter har. Millersippande, köttgrillande och beväpnade konstruktörer i USA väljer helt andra dimensioner på sina damasker än sömnframkallande, humorlösa och gråklädda Düska ingenjörer.
Det ser helt enkelt mörkt ut och funderingar kring hur man tillverkar gjutverktyg för damasker börjar mala i bakhuvudet. Även funderingar kring va fan man håller på med egentligen vaknar till liv – alla andra tittar på TV, umgås med vänner eller sover medans en annan sitter och kuckelurar i garaget och försöker sig på stordåd. Kanske dags att bli som alla andra istället?
Bilhelvete.
drivaxlar – kortning
Svårt ämne det här – att korta drivaxlar. Det ses som hilly-billyteknik av många, medan andra alltid berättar om en kompis kompis som körde kortade drivaxlar på sin top-fuel dragster och som höll för ungefär åtta miljoner hästar i 200 år. Helt sant, kompis kompis så de känner typ oftast varandra. Nästan.
I detta fallet kan man se det från en annan sida; Bakvagnen är byggd från blankt papper. Där är inte så många saker som i teorin kan gå snett, men å andra sidan brukar det sällan vara de sakerna man aktivt förebygger utan de oförutsedda som strular i slutänden. Specialtillverkade är relativt dyrt – 6000:- för två stycken.
Att sortera ut bakvagnen tar gissningsvis 50-200 mil kanske innan man har säkrat att allt håller och fungerar som det är tänkt. Då är man sällan uppe i 250km/h. 0-100km/h under tre sekunder förekommer inte heller så ofta. 50-200 mil kan man använda hembygdda drivaxlar, och därefter kan de uppgraderas till specialtillverkade om man inte insett att hela bakvagnen behöver konstrueras om.
Nu behöver nog inte hela bakvagnen konstrueras om – men du fattar säkert – det finns en ovilja i att investera i specialprylar som kanske måste kasseras efter första säsongen. När allt väl fungerar, ska jag köpa drivaxlar som får Formel1-teamen att kännas som amatörer. Om man nu kan få sånt för 6-7kkr…
Ovan; En rad olika tekniker gicks igenom och via internet försökte förstahandserfarenhet sållas ut. Verkar som att vanlig V-fog och pinnsvets är en ganska tillförlitlig metod då pinnen skapar en förhållandevis mjuk och duktil fog.
Nedan; Sådärja, inget att be för. bara att såga av axlarna. Innan de kapades, rensvarvades de från tidens ytbehandling – rost alltså. Därefter V-formades de med vinkelslipen. Efter dessa bilder ökades V:et till ca 30mm/axel. Dvs fogen blev totalt 60mm bred – många svetssträngar blev det innan den var fylld.
Nedan; Svetsad och grovsvarvad. Rotation med indikatorklockan för att hitta var den slår (drivaxlarna svetsades spända mot en V-profil, men de slår sig lite ändå). När läget var lokaliserat, flyttades drivaxel och indikatorklocka över till pressen där den justerades. Det blev några vändor fram och tillbaka, men till slut slog de på mindre än tre hundradels millimeter.
Nedan; När axlarna inte slog längre, var det bara att svarva det sista och därefter slipa med smärjelduk tills att skarvarna försvann. Notera märket på svarvchucken för att alltid spänna in den i samma läge (eftersom den åkte fram och tillbaka mellan press och svarv).
Högra bilden, någon enstaka por här och där avslöjar att man meckat med axlarna, men annars är det svårt att se.
Nedan; Färdiga axlar, i väntan på lite färg. Så klart gick ett av clipsen som låser axlarna av vid demonteringen. Axlarna är Amerikanska (Ford 8.8-klump, Lincoln axlar). Jänkelandet har ju ”viss” fokus på stela bakaxlar, varför utbudet av delar till 90-tals delade bakvagnar är… obefintligt.
Mer raljerande kring obefintliga reservdelar och svart bälte i Google kommer inom några veckor. Det här är inte sista posten om drivaxlarna, tyvärr.
Drivaxlar
Eftersom drivaxlarna inte kan vara originallängd gjordes två tolkar för att enkelt kunna prova fram längder. Därefter har ett helt gäng inställningar på panhardstag, samt min- maxfjädringsväg testats innan längden slutligen spikats. Lite plats har lämnats för att inte drivaxeln skall riskera att bottna i inneränden (vänster på bilden nedan) pga flex i bussningar och material.
Ovan; Exotiska material används till prototyptillverkningen… VP-rör (PVC antar jag?), rostfri skruv och slangklämma (som om det egentligen skulle behövas) samt ytterändar i någon plast från skrotlådan på jobbet.
Fixturen blev ganska smidig att jobba med – bara släppa på slangklämman och justera längden något. Ytterändarna har flänsar som motsvarar samma flänsar på drivaxeln så längden blir direkt översättbar. Ytterändarna svarvades med någon hundradel i tolerans så att knutarna fick pressas fast (med handkraft).
Ovan; Ganska svårt att få en vettig bild med kameran, men här sitter i alla fall mocken monterad. Därefter var det att prova igenom max in- och utfjädring, med alla möjliga inställningar i sina max- och minlägen. Det blev några kombinationer, men till slut fixades en längd på drivaxlarna som funkade till allt.
På bilden ser man även bromsslangsdragningen med stödpunkt i mitten eftersom slangen annars hängde ner för mycket. Väldigt bra rörlighet i slangen ändå, tack vare att den inte sitter fixerad i stödpunkten, utan kan röra sig fritt (gummiklädd klämma där gummit avlägsnats och ersätts med en svarvad nylonring som träs över slangen).
Diffkåpa
Lite justeringar har fått göras på diffkåpan för att den skulle passa. Bland annat har det stora originalfästet frästs bort och ersatts med en slät plåt. För de två nya upphängningarna fick den ena göras ett litet urtag på diffkåpan också.
Ovan; Nymodifierad kåpa i svart skrud. Det är visserligen aluminium, men den var inte särskilt fin i skicket, så det fick bli färg ovanpå.
Nedan; Så klart satt luftningen precis där bussningen behövde plats. Inte mycket att be för mer än att fräsa bort den och skaffa ett nytt filter. Med lite planering hamnade det fortfarande bakom oljefällan på insidan.
Ovan; Loctites packning är oslagbart. Tyvärr torkar det i röret eftersom användningsintervallet är ganska sällan. Högelastiskt är det dock – ”fnuppen” på bilden lyckades dras ut ur pipen i ett stycke.
Nedan; Kåpan och klump på plats. Måtte den aldrig behöva tas ner igen då det var ganska tungt och osmidig. Även om huset är i aluminium, så väger diffen as (35kg). Rostig magnetisk plugg fick följa med obehandlad – man ska ha något att uppgradera i framtiden också…
Nedan; Därefter stoppades drivaxeländarna i för att kunna mocka upp rätt längd av axlarna. Otroligt svårt att ta vettiga bilder på undersidan av bilen.