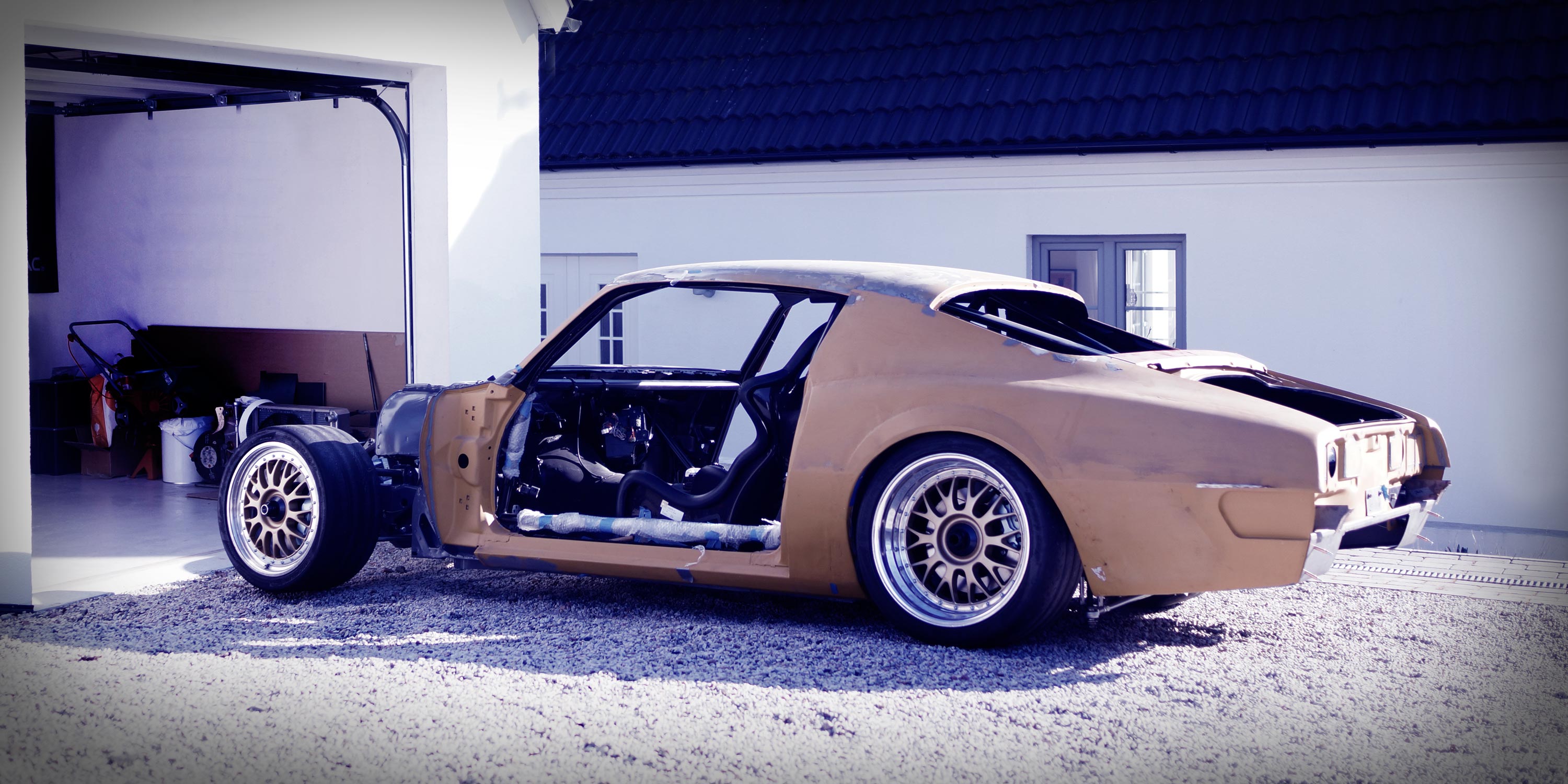
Funkar kommentarsfunktionen?
Eller har bara alla slutat kommentera?
Det har gjorts lite ändringar på sidan för att slippa spam. Men i samband med detta slutade även kommentarerna komma. Numera ekar sidan tom (trots ökande antal besökare).
Inte för att jag på något sätt har bekräftelsebehov. Inte alls. Inget sånt. Alls.
Färg på torpedväggen
Efterlängtad milstolpe! Äntligen är torpedväggen lackad!
Det blev Temadur Polyurethanfärg (precis samma som på underredet), bruten i RAL7015. Under den gråa fägen är det Hagmans CA-V primer, och Hagmans kolfiberspackel (ja, man ska tänka på vikten…), samt en skvätt Hagmans slipgrund/sprutspackel på vissa ytor.
Överlag är det otroligt skönt att ha fått färg på torpedväggen äntligen. Det innebär att subframen nu plötsligt kan monteras permanent, att länkarmar kan börja byggas och att bilen snart står på fyra hjul. Ytterligare ett avslut som markerar att byggfasen av projektet sakta börjar övergå till monteringsfas.
Nedan; Trevlig vy genom bakrutan – burrör och skalstolar – sportigt värre.
Nu får färgen härda någon vecka, och därefter är det pallbocksläge som gäller igen. Dags att montera subframe, framvagnsdetaljer, styrning och bromssystem.
Ytterligare förberedelser
För att måla torpeden måste bilen rullas ut ur garaget (eftersom garaget för alltid annars kommer ha en nyans av senapsgul…)
Eftersom det inte ännu finns några framhjul, och subframen dessutom inte kan vara monterad (svårt att komma åt med färg överallt då…) fick det uppfinnas ett annat sätt att rulla ut bilen på. Tvärbalk i framkant som förstärkning och svivlande hjul kändes som en lagom ambitiös idé, även om plåten vid infästningen var tunn.
Ovan: Lite sprutspackling på de synliga ytorna för att få acceptabel finish. Bara ett lager grund och därefter topcoat och sen är det klart.
Det funkade sådär. Rättare sagt inte alls. När väl karossen kom i rullning, gav offseten mellan hjulaxeln och den roterande infästningen så stora brytkrafter att plåten helt enkelt vek sig. Klantigt och naivt och tro att plåten skulle hålla.
Generation 2 av transportlösning inkluderade hjuldolleys, några träbitar som distanser, skruvar till subframeinfästningarna och en distans för att kunna spänna skruven. Skruven spändes i karossen och skruvskallen hamnade i det borrade hålet i träbiten (för att inte karossen skulle glida av). Denna gång gick det bättre!
Ovan; Version 1 förstörde plåten. Tack och lov gick den att knacka tillbaka. Även om det inte är synlig plåt, är det skönt att veta att plåten är rak och fin. Högra bilden visar version 2 (som höll betydligt bättre.
Förberedelser inför torpedmålning
För närvarande läggs tiden på förberedelser inför målning av torpedväggen. Lackboxen är moder natur, och hon är på väg att stänga boxen för säsongen snart så tiden är knapp. En vindstilla dag med bra temperatur behövs.
Innan dess är det dock underarbete som finns att göra. Ett lager grund lades igår och nyss hamnade ett lager slipgrund på torpeden. Förberedelser under helgen och förhoppningsvis blir det målning under nästa vecka.
Ovan; Det blev ett par snabba bilder från gårdagen när bilen var på väg tillbaka in i garaget. Klockan var mycket, det var mörkt och ganska kallt ute. Egentligen inte alls sugen på att springa runt med kameran, men en bild är bättre än ingen bild…
5 sekunder slutartid gör att maskeringsplasten som fladdrar i vinden ser dimmig ut.
Nedre länkarmar
Det börjar som ett litet plockepinn. Alla standarddetaljer – länkhuvuden, spindelleder, bussningar, skruvar etc – köps hem. Därefter svarvas hylsor till bussningar, rör kapas i rätta vinklar och gängade hylsor till länkhuvuden svarvas. Plåt skärs och kantas.
Därefter är det das att tillverka en stabil fixtur – länkarmar är, och ska vara, förbrukningsvara. På så sätt slipper man förhoppningsvis reparera saker på ramen vid en eventuell smäll. I detta fall fungerar fixturen både till övre och undre länkarmar.
Notera att rören är plattovala, 40x20mm. I ärlighetens namn är det för att det ser coolt ut. Det här är en karossbil, så någon aerodynamisk fördel ger de knappast. Dock borde de vara något styvare än 30mm runda rör vid retardation. Eftersom pushrod-infästningen sitter långt ut på armen, påverkas inte själva armen nämnvärt av fjädrandet. Planen var från början att ha pushroden monterad direkt i spindeln, något man ofta ser på formelbilar. Fördelar är bl.a. att det avlastar spindelleder, länkarmar kan göras lättare mm. Tyvärr är det svårt på gatbilar pga det större styrutslaget (+-35° jämfört med gissningsvis +-15)
Dåligt tempo
Tanken har säkert slagit dig – inga uppdateringar på länge innebär sannolikt att projektet har gått samma väg som många andra stora projekt; Självdöd pga andra saker i livet som tar tid eller pengar…
Riktigt så illa är det inte. Sommarmånaderna har inneburit jobb på annat håll vilket har gjort att garagetiden har lågprioriterats. För närvarande väntas det på rätt tid för att kunna lacka torpedväggen.
Allting är förberett. Bilen är maskerad och målningsutrustningen framtagen. Nu ska bara tiden och rätt väder tajmas också.
Rattstång och elservo
Infästningen för Elservot är äntligen klar. Varken laserskuret eller CADat, utan skapat på fri hand. Vedbobygge med andra ord. Trots det blev det rätt bra.
Ovan: Vänstra bilden visar kontrollenheten för servomotorn. Eftersom den är CAN-styrd beroende på hastigheten, får man köpa en liten styrning till kontrollenheten (svarta lilla plastlådan på kontrollenheten). Potentiometern på bild ger justerbar servoverkan (från 0-100%), vilket är en trevlig option. I regn kan man tex ställa ner servot och framför kiosken kan man vrida upp det för att inte få mjölksyra när det skall fickparkeras.
Nedan; Kändes smidigt att kunna plocka med blinkers- och helljusspak. Inte säkert att de kommer användas i dagsläget, men som sagt skadar det inte att ha liggandes på hyllan.
Nedan; Och så här blev det. Pga de ökade krafterna som blir när servoverkan flyttas från styrväxeln till rattstången, sitter det infäst i originalinfästning (samma som pedalstället) och även klämd runt buren. Tack vare att det är fäst i buren, styvar det inte bara upp rattstången, utan även pedalstället. Torpedväggen kommer flexa radikalt mindre, vilket resulterar i en stum och fin bromspedal. Win-win med andra ord.
Diffklump
Det droppade in en del frågor om vad det var för diffklump som används i bygget.
En Ford 8.8 med aluminiumhus från en Lincoln Mark VIII är det som används. Den förekommer även i Thunderbird, men då i gjutjärn om jag inte minns fel. Även Cobra-versionen av Mustangerna har denna.
Ovan; En del ford-prylar smyger sig in på bygget… Både bakaxelklump och styrväxel är Ford. Bakaxelklumpen har snabbsminkats med Pontiacskuren plåt.
Nedan; Utväxling är i det här fallet 3,73:1. I förra generationen av Pontiacen, kördes den med 4,56:1 och tillsammans med T56-lådan funkade detta väldigt bra. Ettan blev väldigt låg dock. 3,73 ger lite längre etta och ett ganska bra register upp till fyran (1:1). Femman funkar bra på landsväg och sexan går väl knappt att få i under 130km/h…
Diffkåpan har fått modifieras lite för att passa med dedionen.
Infästning för kylarram
Det mesta är klart på framvagnen nu. Så även infästningar för kylarramen. Kylarram, samt kraschboxar är tänkta att skruvas i mot delarna på bilden. Om det går att få till två vettiga kraschboxar återstår att se – inget är CADat än, men allting går ju…
Nedan; Infästningarna jiggades (såklart!) får att förhållandet mellan dem skulle vara exakt. Därefter är det enkelt att rita upp en vettig kylarram.
Kaross x (diffklump + dedion) = Passform?
Ovan; Ett försök att vädertäta länkarmsbussningarna har gjorts. I detta fall med det fantastiska och väldefinierade materialet ”cykelslang”. Just cykelslang brukar (endast i detta fallet, aldrig när det ska lagas punktering) ha den unika förmågan att vulka fast i det mesta. Förhoppningen är med andra ord att den med tiden kladdar fast i metallbussningen.
Nedan; Såklart är det inte 100% vattentätt, men det är i alla fall dammavvisande och stänktätt. Betydligt bättre än helt öppna bussningar med andra ord. Plastbuntbanden hoppas jag kan bytas mot något bättre på sikt. Tills vidare får det funka.
Nedan; Tredje länken monterades med hjälp av fyra händer. Skruven sticks i inifrån kupén, men någon måste ligga under bilen och hålla i länkaget. Förbannade konstruktörer – att de alltid ska krångla till det…
Ovan… och nedan; Med tredje länken monterad, provmonterades diffklumpen i karossen för första gången. Platsbrist mellan diffkåpa och dedion har skapat flera millimetermätningar på karossen, fullskalautskrifter av ritningar som måttades mot karossen och en rad andra sätt för att försöka säkerställa att sakerna inte skulle krocka med varandra när de väl kom på plats. Som skrivits innan är det alltid svårt när delar från verkligheten som är för komplexa att rita av (karossen…) ska linjera med konstruerade detaljer från datorn. Det är svårt att hitta lämpliga referenser, svårt att mäta exakt och symmetrin mellan höger och vänster sida på karossen är ofta obefintlig.
Men fega pojkar får aldrig pussa vackra flickor och bilbyggare som aldrig chansar är… öh. töntigt.
Hur som helst – det passar! Med kortast möjliga länkarmar är det ca 7mm frigång mellan diffkåpa och dedion – trots plåtförstärkningen som spontansvetsades på bakaxeln utan att tänkt igenom vad som riskerade att hända med utrymmet. För att hjulen ska sitta rätt i hjulhuset, kommer länkarmarna vara ca 20mm längre än i testläget, dvs där kommer finnas gott om plats för både bakvagns- och karossflex. Win med andra ord!
Nu blir nästa punkt att provfjädra dedionen för att se att det inte tar i någon annanstans.
Gaspedal
Man ska inte försumma de små detaljerna… Känsla i ratt, pedaler och växelspaken är såklart något av det viktigaste på hela bilen…
Ovan; Även gaspedalen har fått en översyn. Det var typiskt fabriksglapp i alla leder vilket såklart behövde ordnas till. Original plast-pedal har fått ge vika för rejsig aluminiumpedal istället (som uppenbarligen inte är med på bilden…)
Nedan; Det fanns både axiellt glapp och radiellt i leden till vänster. Det axiella var enkelt att åtgärda med en bricka (fjädern på andra sidan pressar dessutom axeln lite lätt mot brickan, vilket gör att det blir nollglapp trots låg friktion). Radiellt fick hålet genom pedalarmen brotchas upp till ett metriskt. Därefter svarvades en mässingsbussning som pressades i axeln och i sin tur bearbetades till någon hundradels spel mot axeln. Resultatet blev riktigt bra!
För att kunna justera pedalen i rätt vinkel mot golvet, ordnades en liten justerskruv på pedalaxeln.
Nedan; Jag vill helst slippa allt för mycket skruvar på torpedväggen. För att göra detta, ordnades en adapterplatta mellan torpedvägg och gaspedal. Ett fäste för gaspedalsfästet med andra ord. I denna svetsades M6-skruv som skallarna skars bort på för att få en slät undersida.
Originalglappet togs bort med hjälp av kopparshims som lades mellan plattan och pedalarmen. Glappet blev inte riktigt noll här, men bra nära.
Överambitiöst kanske? Men gaspedalen är ju halva känslan av bilen! 😉
Subframe, igen
Veckans jobb på framvagnen. Det mesta börjar bli färdigt nu.
Ovan; Anpassningar till befintlig ram kräver lite extra detaljer här och där. Gamla urtaget för styrväxeln har delvis fått läggas igen. Som om det skulle användas igen… Högra bilden visar att det faktiskt börjar bli klart – vipparmsinfästning och fästen för övre länkarmar.
Nedan; Vipparmsinfästningarna har svetsats både från in- och utsidan. Rejäl V-fog på utsidan och lika-bra-att-svetsa-här-också-fog från insidan.
Nedan; Även rambenen är numera svetsade som de ska.
Bara interfacet mot framtida kylarram kvar, sen är det dags för grundfärg!
Svetsning…
Det blir tämligen många meter svets när man håller på med plåtkonstruktioner… Vill inte riktigt räkna efter hur mycket det rör sig om, men det har uppskattningsvis tre 50-liters TIGtuber på att bygga fram och bakvagn och ett antal timmar. Bara ”de sista detaljerna” på subframen som pågår just nu har hittills tagit ca 100h att färdigställa. En grov uppskattning säger att byggtiden på subframen är runt 200h. Lägg därtill konstruktionstid i datorn också…
Ovan; Fixturen positionerar både länkarmsinfästningar och vipparmsmontage. Det är väl inte positionering på tiondelen med tanke på att det är vanliga fyrkantsprofiler, men det håller betydligt högre toleranser än vanliga biltillverkare gör på sina saker.
Nedan; Hade nästan vant mig vid att se ramen utan infästningar…
Coil over-infästningar och krängningshämmare
Lite prylar behövde tillverkas för att komplettera ramen. Infästningar för coil-overs och vipparmstornen.
Ovan; Börjar bli ganska bra kompis med TIG:en nu. Men å andra sidan har det spenderats ett par hundra timmar bakom den, så konstigt vore annars. Bilden visar infästningarna för stötdämparna. Samma princip som bak, dvs ett öra som håller coilovern (skymtar längst bak i bild) och som sedan kan flyttas fram och tillbaka på subframen beroende på längd på coilovern. På så sätt är det enkelt att uppgradera i framtiden utan att behöva göra stora ingrepp i chassiet.
Nedan; Krängningshämmare har det funderats på ett tag nu. Vanliga rörklamrar köptes från Swedol som lagerbockar. Därefter svarvades ändavslut (notera flänsen för att inte krängningshämmaren skall glida i sidled) som sedan parades ihop med ett 40x2mm rör. Ja, 40mm i diameter. Planen är inte att låta röret ta vridningen, utan istället tillverka knivar och därmed isolera rörelsen till dessa.
Nedan; Ytterligare en bild på coil over-infästningarna. Översta har även coil over-örat ställt ovanpå sig för att illustrera justerbarheten. 3 lägen totalt med 25mm mellan varje. 75mm längre/kortare dämpare kan med andra ord få plats.
Vipparmshylsorna fick så klart svarvas ur då de annars hade blivit löjligt tunga.